Built to Move: Trends drive construction of athletic facilities
From elite performance facilities and college gymnasiums to pickleball courts and downtown fitness centers, strong demand for athletic facilities is providing contractors with a supply of routine and extraordinary projects.
On the shores of the Chester River, Gipe Associates was tasked with designing the mechanical/electrical building systems in a unique structure — a state-of-the-art, highly sustainable boathouse and training facility.
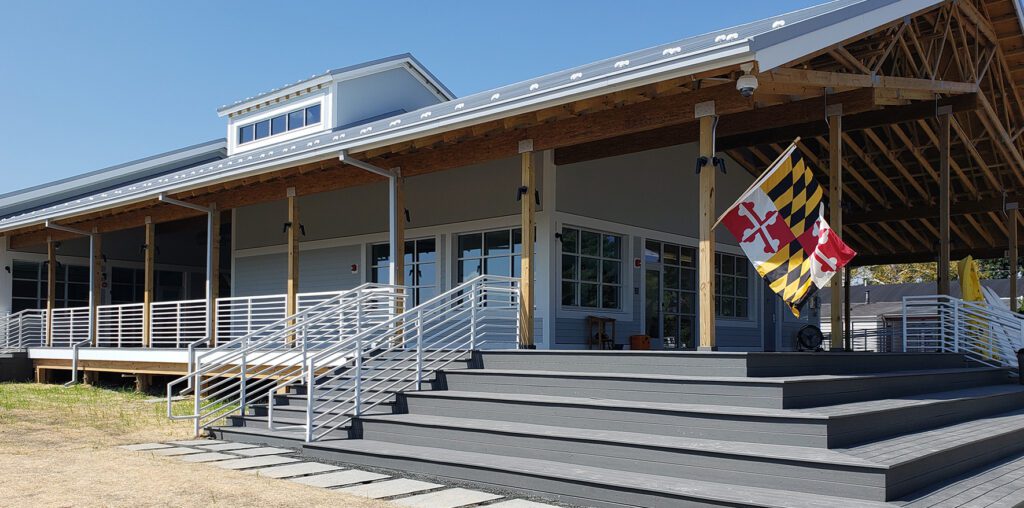
The Hodson Boathouse project was designed to establish Washington College as a top destination for rowing and sailing student athletes. Photo courtesy of Gipe Associates.
A goal of the Hodson Boathouse project was to create an elite training facility that would establish Washington College as a top Division III destination for first-class rowing and sailing student athletes. The design for the 12,000-square-foot building included an expansive cardio workout room, a 35-seat classroom, team lounge, locker rooms, offices, and a covered, wrap-around, 3,675-square-foot deck.
It also included a feature that Gipe Associates President David Hoffman had never encountered in his more than three decades of engineering experience – a state-of-the-art rowing tank room. Outfitted with a 16-station, 25-foot by 54-foot rowing tank, the room was designed to enable teams to perfect their sweep and practice during inclement weather.
That unique blend of functions within the building combined with the sensitive nature of the riverside site and the client’s sustainability goals compelled Gipe to design an unconventional yet simple mechanical system.
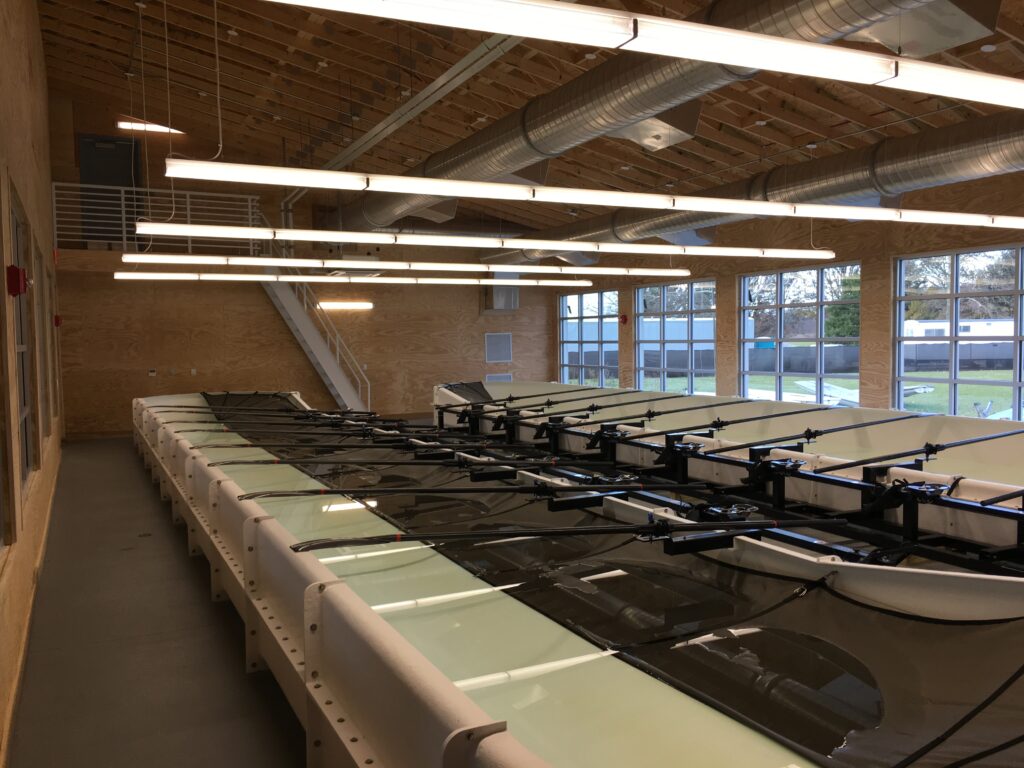
The building systems at Hodson Boathouse had to support a variety of uses, including offices, locker rooms, a cardio room and a state-of-the-art rowing tank room. Photos courtesy of Gipe Associates.
“One key design component was to have the ventilation air separate from the space conditioning air — a decoupled system — so the fresh air and exhaust is a separate unit from the unit that heats and cools the spaces,” Hoffman said.
To achieve sustainability goals and avoid having fossil fuels near the river’s floodplain, Gipe opted to heat and cool the building through a closed-loop geothermal system. The mechanical design also provided a unique, robust solution to the rowing tank room’s dehumidification needs.
“Because it is basically an open tank of water, we looked at the rowing tank area as an indoor pool. So, we utilized a pool dehumidification unit that is a geothermal water-source unit which means it ties into the geothermal system,” Hoffman said. “That makes it extremely unique. We are taking the heat from the dehumidification and dumping it into the ground. Then in the wintertime, that basically becomes free heat that we use to heat the building.”
The building systems also helped achieve the client’s goal of creating a showpiece and gathering space on the river.
“With this building, aesthetics were extremely important and the architect did a beautiful job,” Hoffman said. “Not ruining the aesthetics was the biggest challenge from our perspective. We have the things that are ugly, the things that make noise, the things that vibrate. We had to incorporate those without ruining the architecture on this beautiful, waterfront setting. I think geothermal was a home run in achieving that.”
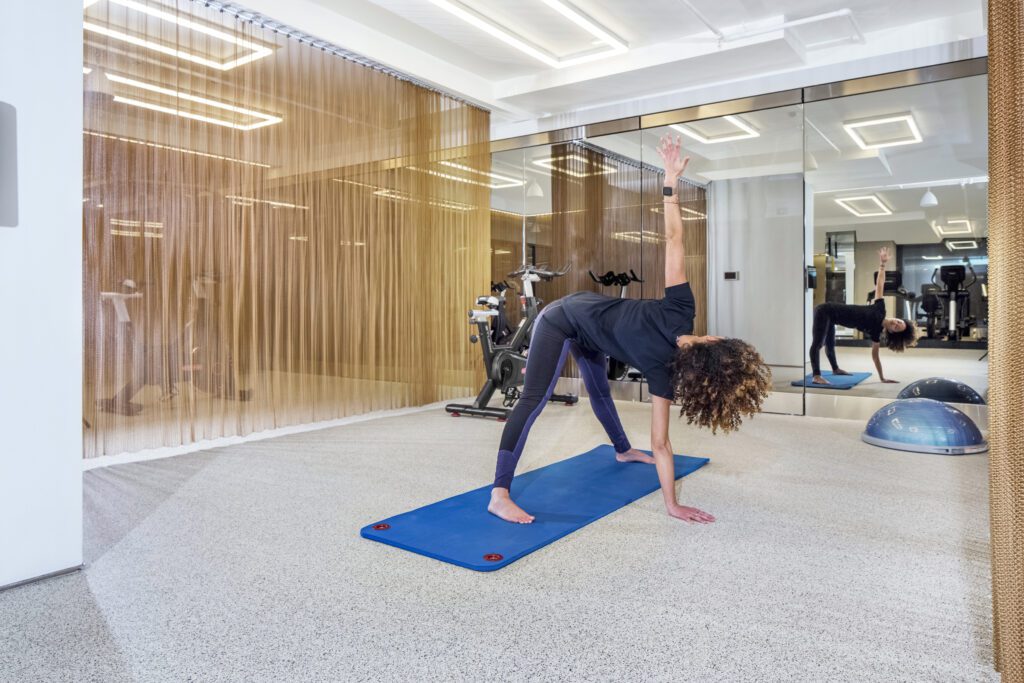
Efforts to entice workers back to offices have convinced some building owners to transform space — including underground parking — into lavish fitness centers. Photo courtesy of DPR Construction.
In a much different environment, DPR Construction has been meeting a current trend in athletic construction and the challenges that come with it.
The drive to attract tenants and employees back to office buildings has prompted many building owners to renovate and repurpose space in order to create extensive amenities, including high-end fitness centers.
At 1801 Pennsylvania Avenue in D.C., DPR created a lavish, Gensler-designed fitness center, complete with workout rooms, extensive equipment, locker rooms, restrooms, sleeping pods and a napping area.
Furthermore, “the level of finishes was uniquely impressive,” said Bill Hahner, Preconstruction Executive at DPR. “Every wall was covered with custom mirrors or back-painted glass. The TVs were all behind mirrors so it looked like a mirror unless the TV was on.”
Other areas were adorned with bronze curtains, he added.
The challenge for DPR was to create that lavish space in a parking garage beneath the building.
“The fitness center was located four stories underground,” Hahner said. “Demolition of the slab-on-grade and lower levels was needed to accommodate the high ceiling heights.”
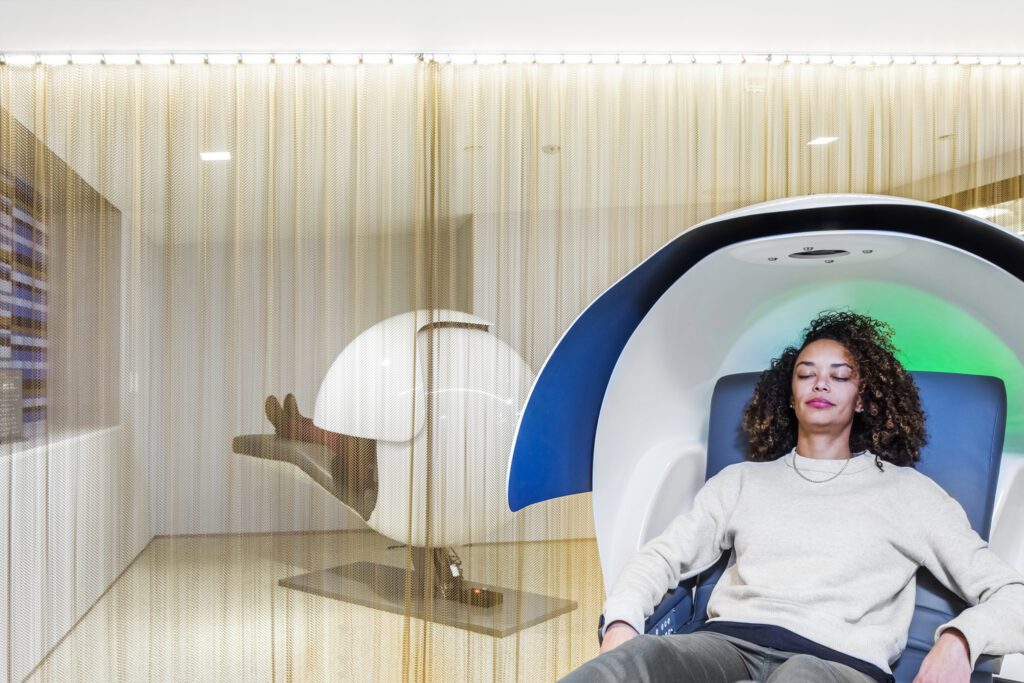
In addition, “being an underground facility, the only access for materials was down the parking ramp which required unique site logistics to ensure the safety of workers and materials,” he said. “Our teams leveraged laser scanning and VDC models to ensure the design worked within the space.”
Repurposing of other commercial real estate spaces has provided Ruff Roofers with a stream of business.
“I keep coming across all these projects that have pickleball in the description,” said Spencer Jacobs, Vice President of Service.
At least five times in the past year, crews from Ruff Roofers have transformed portions of industrial or flex buildings into pickleball centers, ranging from small amenity spaces to large, athletic centers with more than a dozen courts.
Jacobs said the projects are fairly routine and typically focus on making roof modifications to accommodate additional HVAC equipment required by the pickleball facilities.
Ruff’s more challenging athletic projects tend to involve gymnasiums for K-12 schools and colleges.
Due to the roof span, gymnasiums require robust commercial roofing systems.
“Because schools need these facilities to last a long, long time, we are doing almost a ‘bullet proof’ system,” Jacobs said. “You are doing three or four layers of roofing, not just one, to make sure there are no leaks and make sure the school gets the full term of the roofing system whether that is 15 or 20 or 30 years.”
Delivering that extremely tight system requires special efforts.
“Our biggest concern is always the flooring underneath us,” Jacobs said. “Gymnasium floors are immensely expensive and if a floor gets ruined by a leak, that is a major, major impact.”
So, on every gymnasium project, Ruff assigns an extra supervisor to review site conditions, especially at the beginning and end of each day, to ensure that nothing is left exposed. Ruff also directs extra effort to educating clients about the critical need for regular roof inspections and maintenance.
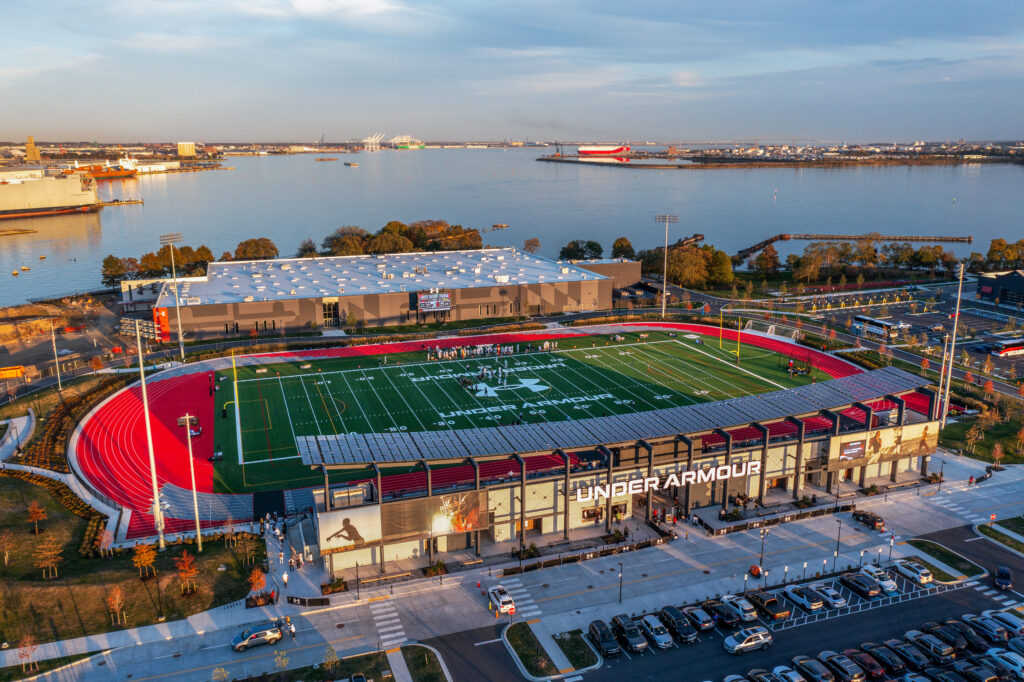
Multiple BC&E companies helped build the signature Under Armour Track and Field Facility, which includes a competition track, multi-dimensional field and advanced technology to track athletes’ performance. Photo courtesy of Under Armour.
“Every single system requires regular maintenance, and every manufacturer includes that in their warranty” Jacobs said. “A lot of sealants and caulks only have a five- to 10-year lifespan. You have to be up on the roof every year, making sure all your sealants are in good shape, making sure all your drainage systems are clear. I have seen it thousands of times that a water bottle gets dropped on a roof, washed into a drain, then the drain backs up and sends water into the roof.”
Then every now and again, an athletic job comes along that is anything but routine.
Construction of the Under Armour Track and Field Facility involved a bevy of BC&E member companies: The Whiting Turner Contracting Company, Excell Concrete Construction, Henry J. Knott Masonry, Baltimore Fabrication, Walls and Ceilings, Ariosa and Company, and Live Green Landscape Associates.
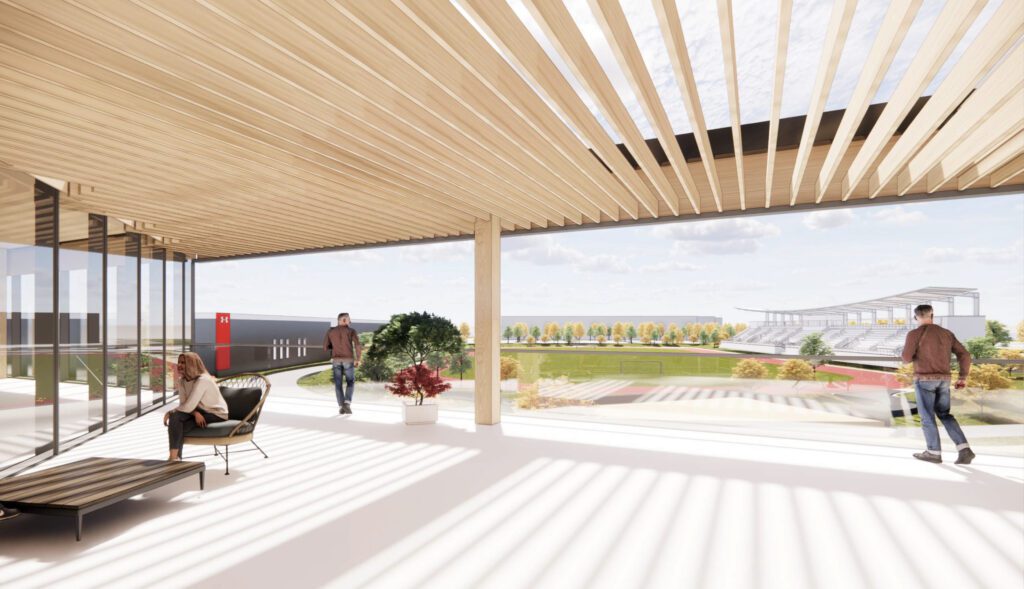
Together, the project team created a state-of-the-art, signature facility that includes an eight-lane, 400-meter competition track and seating for 1,400 fans. Its multi-dimensional field is designed to support a range of sports, including regulation high school football as well as NCAA and high school soccer and lacrosse.
Under Armour also plans to use the venue to test its products in the pursuit of new levels of athlete performance. Consequently, the facility is outfitted with leading edge technology that can track and measure athletes’ performance in real time.
The facility also had to blend with the high sustainability standards of Under Armour’s new headquarters on Baltimore Peninsula.
“Our new campus is a physical expression of our brand’s commitment to this community and to our core values – including to act sustainably and love athletes,” said Kathy Blessington, Vice President of Real Estate.