Making a Splash
From a rooftop pool overlooking a city skyline to a community pool awash with neighborhood kids, swimming pools are some of the best loved construction projects come the height of summer.
Fortunately, a few market trends — including the desire for more amenities in multifamily developments and the commitment of some local governments to create more public recreation facilities — have been generating a string of swimming pool construction projects.
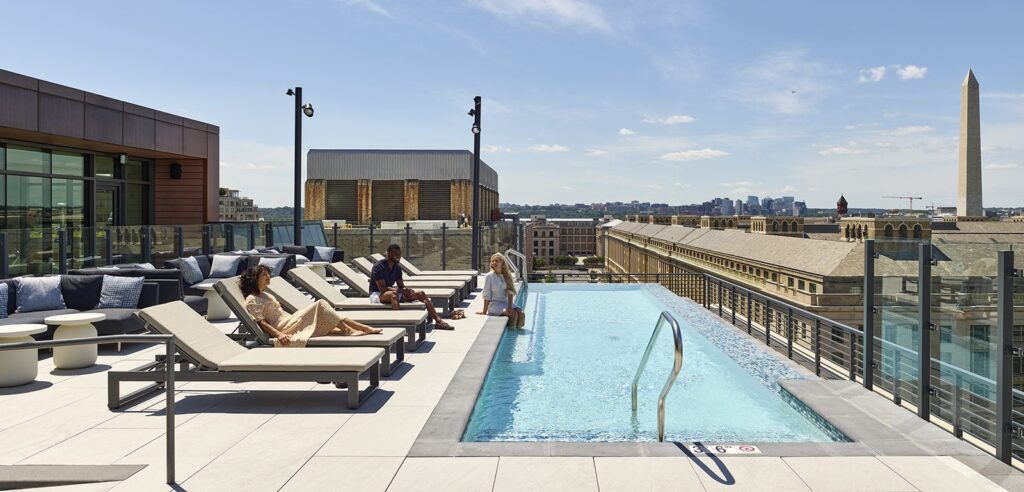
While designing The Annex on 12th, a 562-unit multifamily development in Washington, D.C, Design Collective was asked to include a luxury pool on top of the 13-story building.
As with many rooftop pools, space was at a premium. In addition, designers had to overcome a list of technical challenges involved in building on the structure; drainage, height restrictions, safety requirements and MEP systems needed to operate the pool.
“It’s an exercise in mind gymnastics to understand the technical constraints of the building while balancing the spatial needs of the project,” said Brian Reetz, Principal with Design Collective. “Big picture decisions need to be made early in the design process about the pool and unit counts, and balancing those two… In some developments, you can’t lose two apartment units beneath the pool because that won’t work with the project’s pro forma.”
A decision to retain apartments beneath the planned pool at The Annex meant designers had to alter the elevation of the roof to accommodate the full depth of the pool and the systems that needed to run beneath it. The design also had to comply with the Americans with Disabilities Act and Washington’s tight building height restrictions.
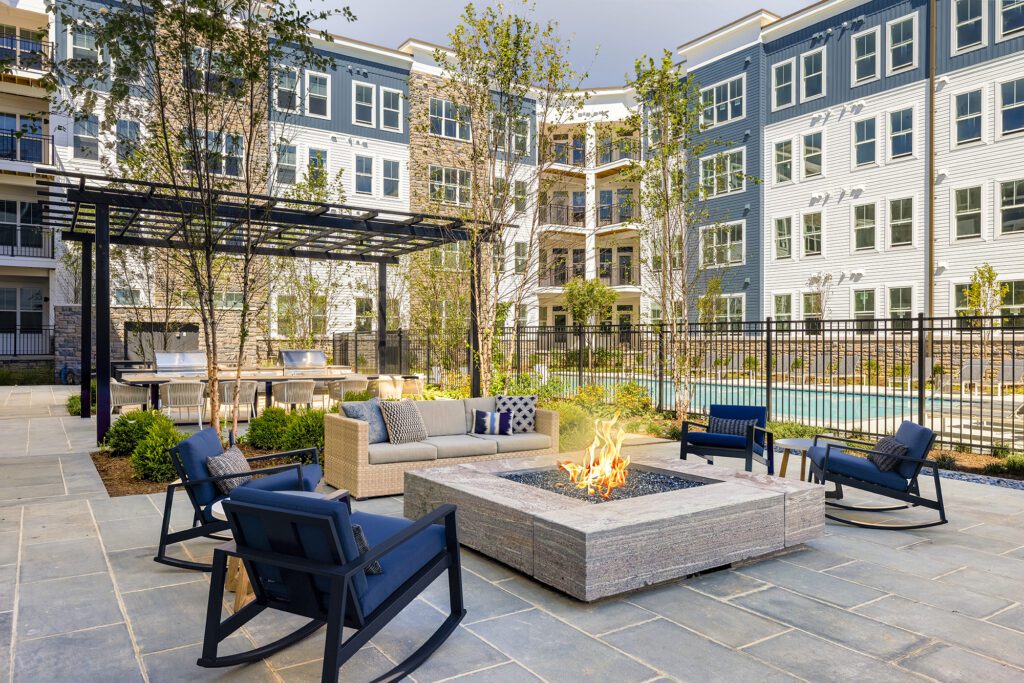
The solution to all of those challenges was to install a modest, four-foot deep, infinity edge pool at one corner of the rooftop. Set in among chaise lounges, other seating options, the building’s clubhouse, planters, a four-seasons outdoor space and a clear glass safety fence, the pool provides residents with a luxurious opportunity to take a dip, sun bathe and socialize in front of a spectacular view of the Washington Monument.
The monument, Reetz said, “is a borrowed visual amenity. It’s a very Japanese design theory. You design your space to borrow views and that makes your property more amazing.”
Other multifamily pool projects aren’t as technically challenging, but no less carefully crafted.
At The Forge apartment complex in Elkridge, Design Collective created a more spacious pool in a ground-level courtyard. The design included laminar jets along one side of the pool to create soothing white noise and a resort-style chaise lounge shelf at one end of the pool where residents could recline and drape their feet in the water.
Pools, however, are only part of the “checklist of amenities that are needed to woo potential renters,” Reetz said.
“You’re selling a lifestyle so you need interior amenities that complement exterior amenities, and the quality of amenities can make a project stand out.”
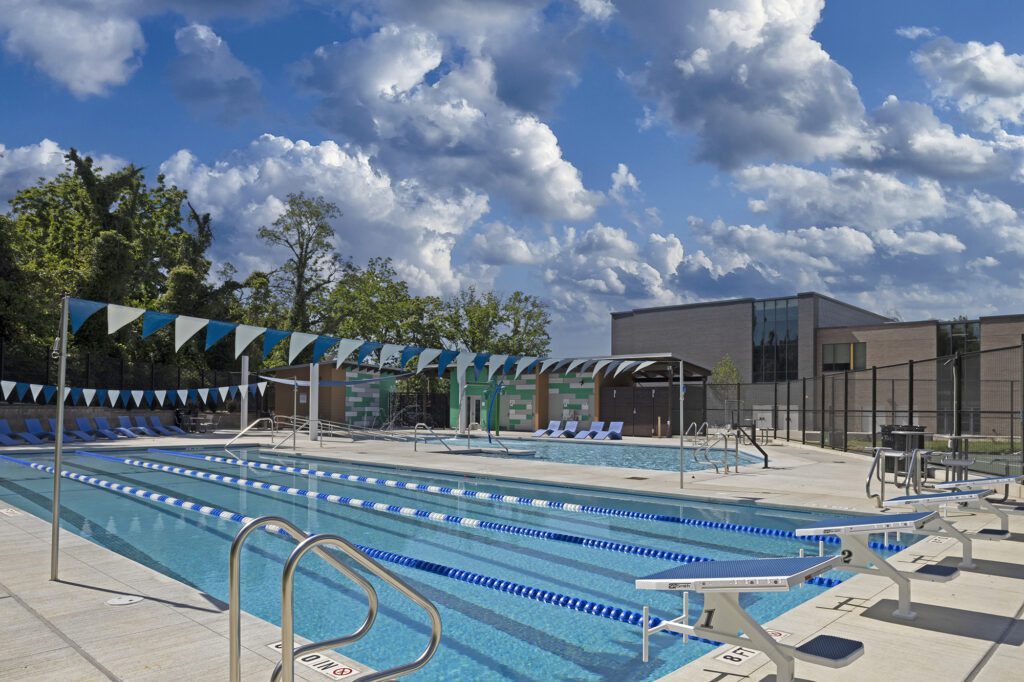
Consequently, The Forge’s pool area was designed to be visible from inside the clubhouse, but surrounded by other attractive features — a four-season outdoor space, community grills, an outdoor TV, a variety of comfortable seating options, and even space that could be used for co-working.
“I’m always surprised at how many people rent an apartment and then work in the amenity spaces,” he said.
Consequently, residents at The Forge could easily settle into a comfy chair in the courtyard or a table beneath a trellis to work on their laptops then refresh themselves midday by diving into the pool for a quick swim.
In Baltimore City, Plano-Coudon Construction is executing a different series of pool projects. As part of the city’s effort to replace aging and sometimes mothballed community pools, Plano-Coudon was contracted to build new pools at Walter P. Carter school, the Towanda and Coldstream recreation centers, and the Greater Model Aquatic Center.
The company which built the Druid Hill pool a few years ago, has been honing its knowledge of the pool-construction niche “so we can make better assessments of project scopes, conduct better upfront negotiations of contracts and be more competitive,” said Grant Cunningham, Project Executive.
That knowledge has also helped project teams navigate typical challenges.
For example, plans for The Walter P. Carter Aquatic Center called for creating a lap pool, a family pool, a bathhouse and a pump room on a half-acre site. A tight site, a tight budget and an acute need to have the pool ready to open by summer meant the project team had to avoid any time-consuming rework, even when they encountered surprises.
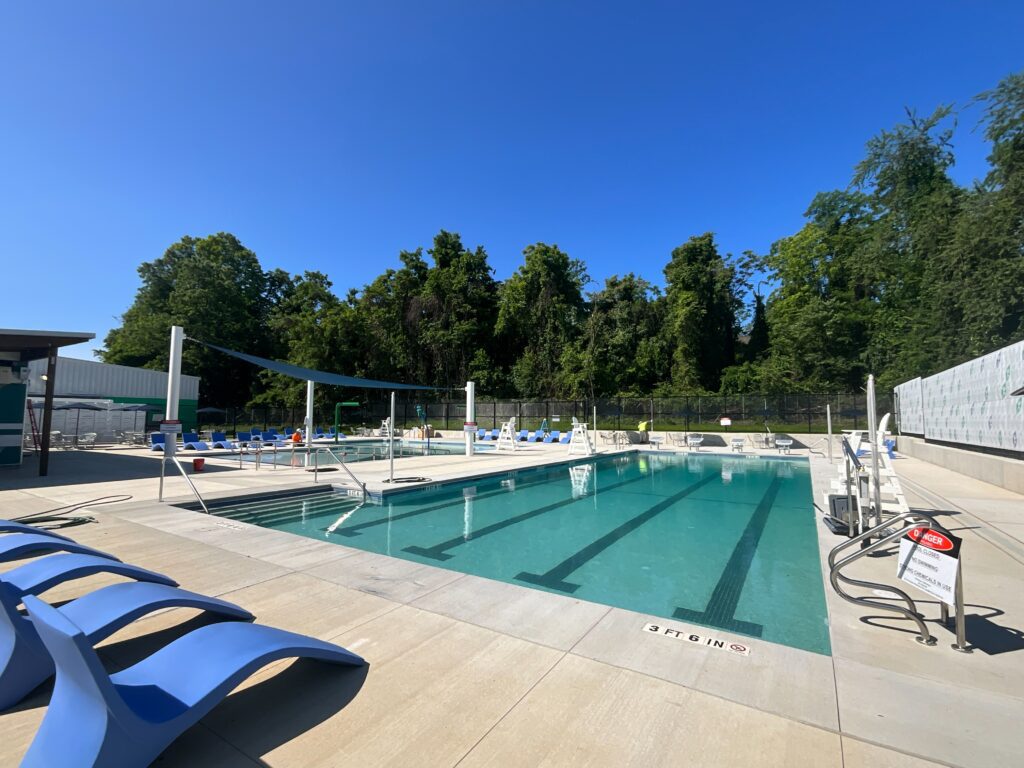
“The most impressive work that happened on this project was underground,” said Rishabh Jain, Project Manager at Plano-Coudon. “There’s so much piping and coordination that needs to happen. You have all the pool piping, supply piping and return piping for both pools looping around the site. There is also the storm drain, sanitary line and electrical lines… Knowledge of the underground utilities, sequencing all the work so you started with the deepest utility first and coordinating with all the subs was really important to making sure the installations were done right. Even a small amount of rework could have messed up our schedule.”
The project team achieved that goal, even after discovering that an existing water line that the new pools were supposed to tie into was actually defunct and carried no water.
Other city pool projects have included additional requirements.
In addition to two pools, a bathhouse and pump house, the Tawanda Aquatic Center project included construction of a new playground and an urban soils restoration project.
“It was a pretty extensive cut and replacement,” said Ben Banbury, Senior Project Manager with Plano-Coudon.
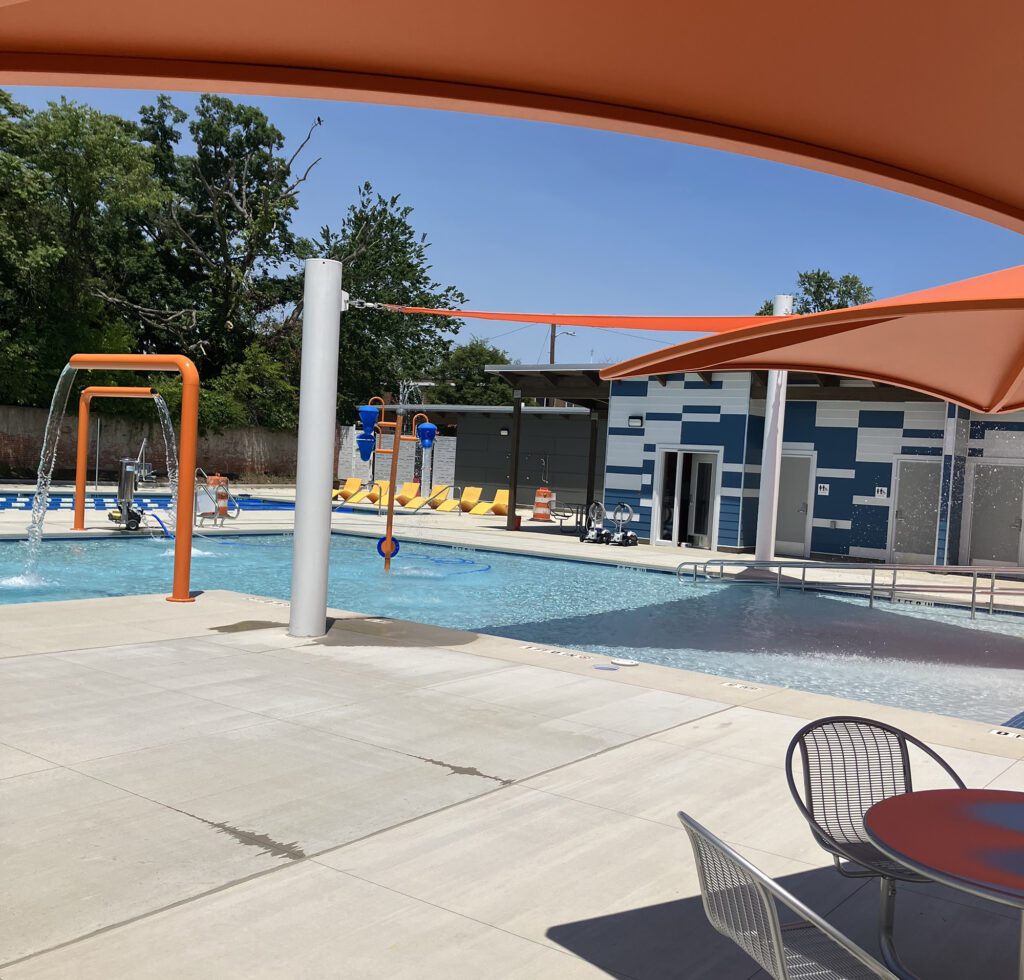
Crews had to remove two feet of soil across a former ballfield then remove rocks, unsuitable soils and other inappropriate subsurface materials, including some foundations they uncovered. Crews screened the soil, added amendments based on soil testing, layered on six inches of new topsoil, and reseeded the field.
To complete the Towanda and Coldstream projects on schedule, Plano-Coudon also had to make some bold, proactive changes to the work schedule which began last fall.
“A cold, wet winter is always a big concern when you have a project that’s dominated by site work and outdoor activities,” Banbury said. “We tried to tackle that by coordinating with the city about working overtime up front in anticipation of weather issues and getting the project out of the ground before the winter months.”
All that work on the community pool projects, however, has delivered special rewards.
The Walter P. Carter Aquatic Center is adjacent to an elementary and middle school.
“Towards the end of the project, kids were coming up to me and anyone else working there and asking, ‘Is it ready? Is it ready?’” Jain said. “You could see the excitement in their faces and how important this pool was to them.”
At the Towanda and Coldstream recreation centers, “I saw kids in swimsuits get on buses so they could go to some other pool to swim one day a week,” Banbury said. “With these projects, we are reestablishing something special in these communities that kids and families will be able to enjoy every day through the summer.”
AI becomes a construction tool
During a recent webinar by the Maryland Center for Construction Education and Innovation (MCCEI), one panelist described the importance of construction companies adopting Artificial Intelligence by quoting American futurist Stuart Brand:
“Once a new technology rolls over you, if you’re not part of the steamroller, you’re going to be part of the road.”
AI is rolling through the business world and many construction industry leaders say companies that fail to productively harness its power will find themselves struggling with a competitive disadvantage.
“If you don’t adopt an AI model to improve your back-end operational efficiency, if you don’t adopt an AI model to improve your front-end sales efficiency, know that your competitors will,” said Kevin O’Brien, CIO at Advance Business Systems. “Then, rather than having a leg up on the competition, you will be fighting to maintain your business.”
That market prospect doesn’t only apply to large construction companies. Increasingly, AI bots, personalized GPTs, data analytics, forecasting functions, and large language models are becoming business tools for mid-sized and smaller firms. And while AI adoption is a major technological advance, it is also becoming easier to implement in small to medium-sized companies.
Yael Meretyk Hanan, Co-Founder and CEO of Pelles.ai and a speaker at the MCCEI webinar, advises trades contractors to approach AI adoption with a business focus, not a technological one.
“Let’s stop and understand where your challenges are,” she said. “What are the things you are looking to improve?… Where are the inefficiencies?”
Meretyk Hanan urges companies to pick one pain point in their operations and begin their AI adoption by addressing that. Even small contractors can afford to develop custom GPTs, which can cost as little as $20 a month, to automate inefficient aspects of their pre-con or back-end operations, she said.
Many companies can leverage software systems they already license to optimize business processes through AI, O’Brien said.
“Everybody seems to have an AI copilot right now. Microsoft has one, Procore has one, Sage has one,” he said. “You don’t have to invest in expensive, new applications. You can, for example, leverage the copilot in your Microsoft 365 Suite to source data and begin optimizing your processes.”
Software companies, IT consultants and other organizations offer training on how to effectively use various copilots, ChatGPT and other AI bots.
Successful adoption hinges on several core activities, including making data accessible often through a data warehouse or data lake, securing data against hackers or inappropriate use, and directing the AI bot to focus on productive questions and use cases.
“The biggest thing to think about when you are using a GPT is your prompts. You want to be sophisticated in your prompts,” said Ricky Venters, a contractor with Hartman Executive Advisors and founder of Success Journey Strategy. “Instead of saying, ‘Hey ChatGPT, give me the answer to this problem,’ ask GPT to help you think through the right questions you need to ask in order to solve that problem.”
That approach of using an AI bot as a brainstorming partner delivers multiple benefits.
It facilitates deeper problem analysis, brings more relevant data into the process, helps prevent AI hallucinations or results based on incorrect or insufficient information, and “it does not infringe on your authority, your thought leadership and your understanding of your business,” Venters said.
“Over the next decade, firms that want to win in the construction industry will need to adopt AI to solve the problems our industry has experienced for decades – too many delays, too little coordination and too much wasted time,” he said.
DPR Construction is already using off-the-shelf products, including ChatGPT and Microsoft CoPilot, as well as some custom AI tools developed inhouse to boost its operational efficiencies.
The company’s efforts have focused on AI use cases that can deliver the greatest benefits, said Hrishi Maha, a Data and AI practice leader with DPR. To date, those have included using large language models to rapidly access information about a workflow or project, and accelerating access to information embedded in construction specifications, RFIs, and other project documents.
DPR’s AI adoption has also tackled a perennial construction challenge, namely staffing levels.
“Working with our preconstruction team and our business developers, we developed an algorithm which helps people predict what staffing will be required for a project,” Maha said. “Based on work we have completed previously, it will estimate the FTEs required and the individual traits needed. It might say you will require two project managers, two schedulers, a safety engineer and two project investigators to execute a job, and it will give a range of hours for those people.”
That prediction, Maha cautioned, isn’t foolproof. “There are so many nuances in construction which AI is not going to know about. But it gives teams a good starting point and, if the AI estimate is different from their own estimate, it will prompt people to assess the situation more deeply.”
DPR, which has been gradually integrating AI-enabled processes throughout its project and business workflows, expects the technology to fundamentally improve performance within the construction industry.
“AI is the next technology frontier… It can change how we do construction,” Maha said. “The result will be time savings for our people, accelerated jobs, better schedules, more predictable outcomes.”
Faster, safer, smarter
How could AI improve your operational efficiencies today?
Smart schedules:
Incite Automation has built AI-supported project management systems that assess tasking for construction projects. The systems know the roles and certifications of each company’s employees. Based on that knowledge and project specifications, it will propose assignments to a particular job.
“It is able to make determinations based on the location of the jobs and the employees, their certifications and past performance,” said Dustin Sitton, Principal at Incite Automation and a speaker at the MCCEI AI webinar in May.
The system, he added, can also generate proposals for the equipment that should be assigned in conjunction with those individuals and propose adding “fluff time” to a schedule, based on the project’s circumstances.
The tasking plans aren’t always 100 percent correct, but they still save construction companies a great deal of time, Sitton said. “I know organizations that use a big, Excel spreadsheet and spend a day, a week or more on resource management. Now they are getting suggestions [from the AI system], making minor tweaks and they are done in an hour or two.”
Safety:
The combination of AI technology and security cameras, drone videos and other surveillance can enhance jobsite safety while also reducing the time needed for safety compliance.
One Incite Automation client employed a “hard hat guy” to walk jobsites and ensure everyone was wearing their hats. Incite linked the jobsite’s network of security cameras to the contractor’s Power Automate program in the Microsoft Ecosystem and trained an AI bot to recognize a person without a hardhat. The system then scanned the site every 30 seconds and alerted the company to any hardhat issues.
Code compliance:
Higher models of ChatGPT are able to answer questions about building code compliance, including what is required in local, international and other codes, and the changes between different iterations of each code.
Preconstruction and back office operations:
In many companies, AI-supported systems are streamlining payroll processing, invoicing, supply chain monitoring, updating of project documents, employee onboarding, and more.
AI is even helping preserve the deep expertise of veteran employees who are ready to retire.
One option is to “record interviews with those industry pros about how they do things, their thinking processes, problem solving, constructability issues,” said Kassy Slaughter, Senior Manager, Industry Transformation at Procore Technologies and a speaker at the MCCEI webinar. “AI can then convert that into a podcast or other training materials.”
Project Profile: Sparrows Point Park
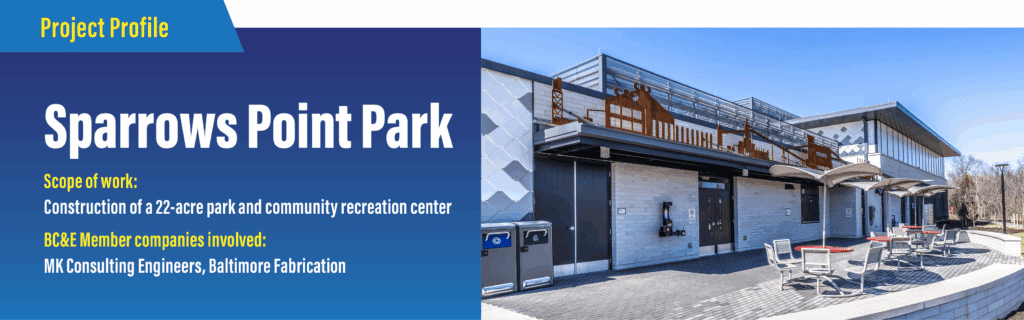
On the site of a former slag heap for Bethlehem Steel, designers, engineers and builders have created an oasis.
The newly opened Sparrows Point Park is Baltimore County’s first LEED Platinum-designed park. It includes a 16,000-square-foot community center, a 10,000-square-foot nautical-themed destination playground, a full-size synthetic turf field with LED lighting, and an ADA-accessible fishing pier and kayak launch.
The site work and landscaping on the 22-acre property has stabilized a shoreline that was rapidly eroding, created scenic water views and gentle walking paths, and set the stage to create a healthy ecosystem on longtime industrial land.
“This property was like a mini dumping ground. There was a lot of stuff left over from Bethlehem Steel’s operations,” said Kristen Gedeon, Senior Associate at MK Consulting Engineers. “There were metal tanks, remnants of railroad tracks and a lot of slag,”
Addressing existing conditions on the property required the project team to meet a litany of requirements.
“We had to get approvals from the Critical Area Commission, the Army Corps of Engineers, the Maryland Department of the Environment and the county. We had to deal with erosion control, stormwater management and site contaminants,” said Steve McCalmont, Principal at MK Consulting Engineers.
Undeveloped areas within the park had to be capped with two feet of clean fill.
“The property has a very steep and eroding shoreline,” McCalmont said. “We learned that the shoreline on that part of the bay erodes at a rate of 1.6 feet per year, so once we cleaned up the shoreline, we put in a stone riprap and revetment to protect that area from erosion.”
Across the site, the team worked to reestablish a healthy and diverse ecosystem. Workers cleared vines and other invasives and planted a half dozen deciduous tree species that are native to Mid-Atlantic woodlands.
In the stormwater management areas, “we added native plants that promote good pollinators,” Gedeon said. “If you have pollinators, then you will get the birds and other small critters. So, we used a mix of perennials and grasses that will come back year after year. Pollinators are attracted to the perennials and songbirds love the little seedheads on the grasses, so our stormwater management is really fostering biodiversity.”
Installing a rare ADA-compliant pier and kayak launch presented the team with a challenge. A fixed pier was not an option. High tides and storm surges could damage it and a fixed pier might not give kayakers consistent access to the water.
Instead, the team had to design a ramp down to a floating pier “but the slope of the ramp could only vary a certain percentage between high and low tide in order to be ADA-compliant,” McCalmont said. “The horizontal geometry for the whole pier, kayak launch and everything was challenging and it was driven by vertical constraints.”
BC&E welcomes three new members
Colliers Engineering and Design is a provider of multi-discipline engineering and architecture, design and consulting services to public and private sector clients developing buildings, transportation facilities and energy infrastructure. www.colliersengineering.com
Founded in 1966, DAVIS Construction serves the Mid-Atlantic and Southeastern regions, building $1 billion of construction annually across 13 diverse market sectors. www.davisconstruction.com
For 100 years, Travelers Bond & Specialty Insurance has been a leader in the surety industry. Travelers delivers contract surety bonds on everything from large work program commitments to the smallest clients in the construction industry. www.travelers.com
Program expands architecture training for city students
As an experienced real estate developer, a trained economist and the son of a Howard University professor, Christopher Flack was troubled to see so few African Americans securing careers in architecture.
Just two percent of licensed architects in the U.S. are Black while Black women constitute only 0.4 percent of architects, according to the National Council of Architecture Registration Boards.
So, in 2021, Flack established the Baltimore City Youth Architectural Design Collaborative (BCYADC) to provide students, ranging from sophomores to seniors, with opportunities to learn design skills and explore careers in architecture.
Through a partnership with Nesmith Design Group and Open Works, BCYADC provides multi-year, after-school and summer training sessions that cover basic and intermediate design and construction principles, AutoCAD, REVIT, code requirements, the fundamentals of residential and commercial projects, and the history of Black Architects in America. The program also requires students to complete their own designs for a residential and a commercial project, and helps students prepare portfolios for college applications.
Last year, the BC&E Foundation awarded BCYADC a $2,000 grant to support that education.
The program is succeeding, Flack said, due partly to its growing partnerships with local architecture firms that help with instruction and offer job-shadowing days to students.
In addition, “students from Morgan State’s School of Architecture and Planning have volunteered to serve as instructors and mentors and help students with their design projects,” he said.
Preparation for the students’ residential project includes a brief historical analysis of Baltimore residential historic designs and housing inventories, and instruction on the use of AutoCAD and REVIT in residential design.
Before graduating from the program, students are expected to develop a residential floorplan, exterior drawings of walls and elevations, and an interior design that includes images of kitchen and dining rooms, a bathroom layout, as well as windows, doors and other details. The students must also demonstrate their designs comply with building codes.
Later in the BCYADC program, students create a design for a commercial project that is reflective of and relevant to the communities where they live. The chosen project (in 2024, it was a community welcome center) must meet the public’s needs, strive to include sustainable elements, and incorporate elements of Baltimore’s history and character.
Students present their designs at BCYADC’s annual Topping Off ceremony.
“This curriculum fully engages the students,” Flack said. “When they get a grasp on the design principles and the technology, they become passionate about sketching and modeling and design.”
The process helps some students recognize the significance of some academic
This spring, eight students graduated from BCYADC and were accepted into college architecture programs, he said.
Positive response to the BCYADC, both from students and architecture professionals, is fueling growth in the program.
In addition to conducting STEM training, modeling competitions and other activities over the summer, BCYADC will be searching for a new, central location for its training in order to become more accessible to students all over the city.
Rising Restaurants: Crews tackle unique dining spaces needs
At a century-old building in the heart of Catonsville, construction crews are working on a project that is complex, demanding and historic.
Founded in 1886 and located at Lexington Market ever since, Faidley Seafood is preparing to set up operations in this new Frederick Road location.
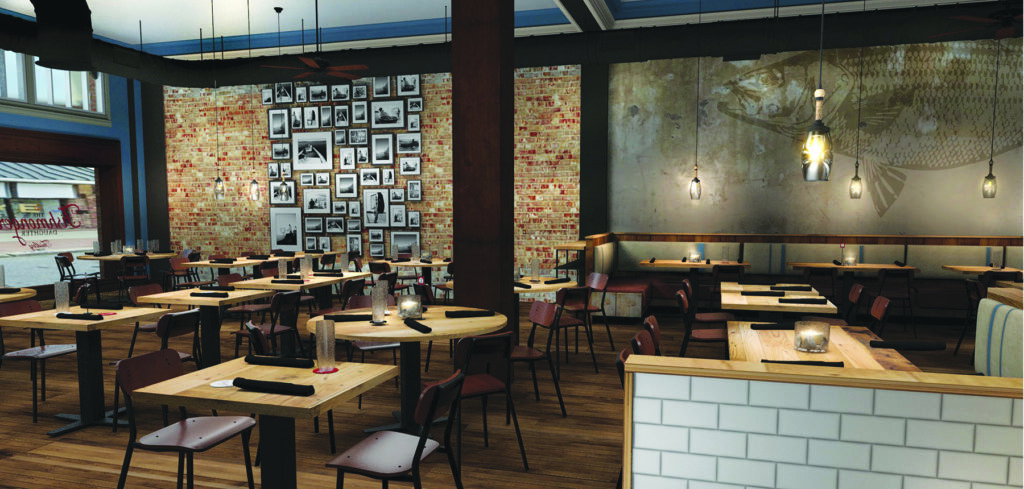
In Catonsville, DACG Commercial is creating a new restaurant for the century-old Faidley Seafood company. Image courtesy of Karlik Design and DACG Commercial.
Even by restaurant standards, it’s a complex project.
The basement is being outfitted to support a major component of Faidley’s business: mail order shipments of its famous crab cakes. The first floor of the former wallpaper store is being transformed into a full-service seafood restaurant, the second into a banquet hall and crews are installing multiple kitchens throughout the building to support those distinct operations.
“This is a huge investment for the Faidley family,” said Taylor Classen, Chief Operating Officer and Partner at DACG Commercial. “They have been in business for nearly 145 years. They want to preserve the family business and help it thrive into the next generation. They see this project as key to that.”
Restaurant projects can demand a lot of designers and builders. In addition to meeting construction schedules and budgets, project teams must craft and execute unique designs, install robustly functional systems, craft welcoming aesthetics, and complete some daunting transformations in order to advance a national brand, meet a chef’s dream or sustain a family legacy.
Challenging sites
With construction happening on three levels of the Frederick Road building, the Faidley’s project has challenged crews to deal with complexities.
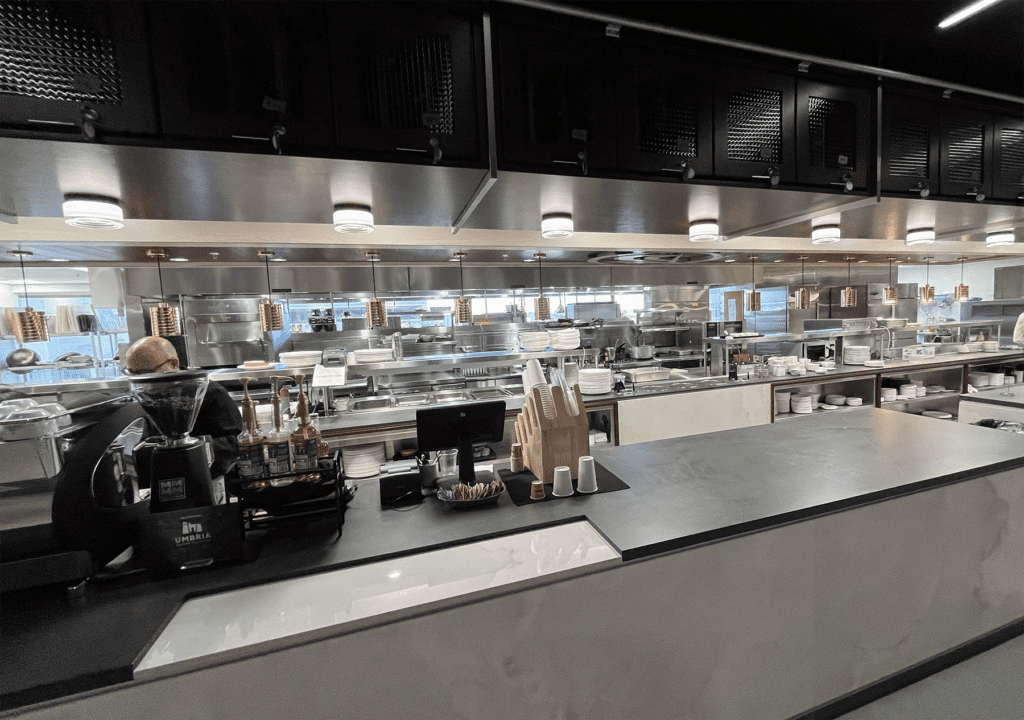
From inviting raw bars to expansive, pristine open kitchens, each restaurant project requires unique results. Image courtesy of Harvey Construction.
“There is different activity happening on each level and we have multiple lifts operating, so it is requiring a lot of coordination,” Classen said.
One surprising discovery made the work even harder.
“Seven months into the project, we discovered that the beautiful limestone front façade had become structurally unsound,” he said. “Now we are removing the whole front façade, supporting the floor system and putting in a new structural support system.
Then we will rebuild the front of the building and, as close as possible, create the same charm and character it had.”
At the Center Club in downtown Baltimore, Harvey Construction navigated a different array of challenges as it worked to complete a gut renovation of a kitchen and dining area. The kitchen was located on the 15th floor of a 35-story high rise.
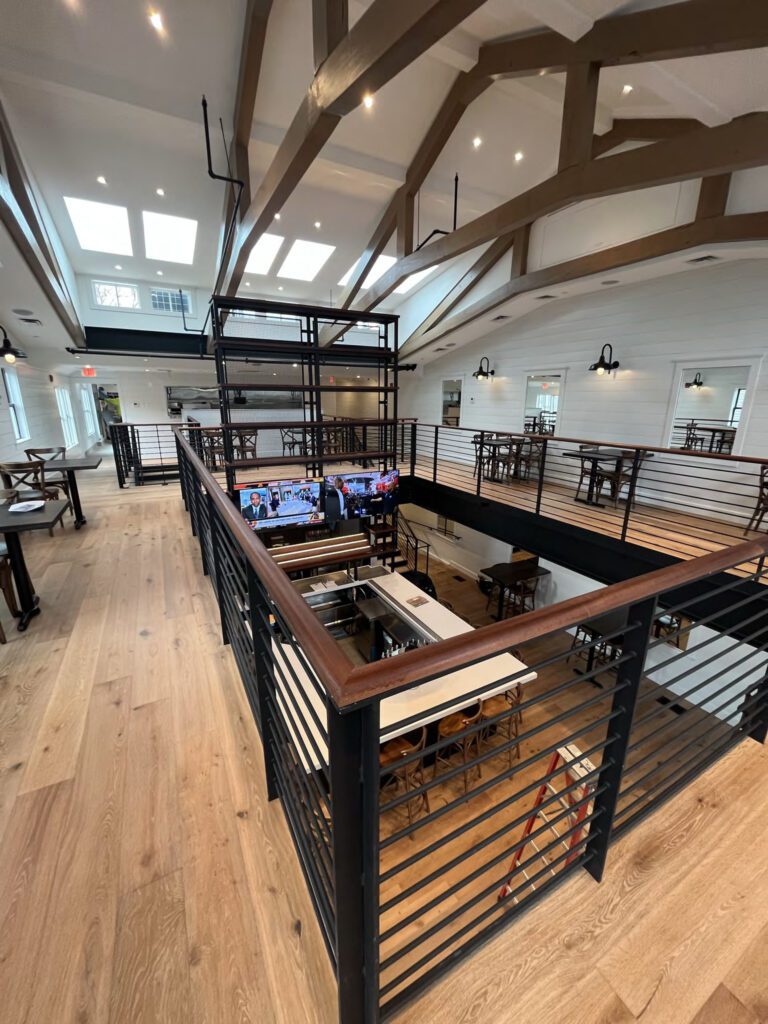
At Adams on Fourth, Harvey Construction built an airy dining space and navigated a space constraint in the kitchen. Photo courtesy of Harvey Construction.
The building had just one freight elevator “and there were contractors working on pretty much every floor,” said Mac Ford, Project Manager at Harvey Construction.
To keep work progressing efficiently, Harvey had to coordinate with contractors leading other projects, and bring its own crews in at 5 am. It also had to push to complete the project on a tight timeline so that the club could get back to full operations and normal revenues.
“There were days when we had 30 contractors in that space, all working on top of each other,” Ford said.
For the Adams on Fourth restaurant in Annapolis, Harvey Construction had barely a year to complete ground-up construction of the building, which would also include two apartments.
High water table in the area created challenges for grading and site work.
“But probably the biggest challenge involved the kitchen hoods,” Ford said. “We had about 12 inches of joist depth in the kitchen so the big challenge was meeting fire rating and fire mitigation with the hoods.”
The project team spent months puzzling through that one element of the project until the team, a third party inspector and city officials agreed on an acceptable hood installation.
Fine dining environments
The results of challenging restaurant projects, however, can be stunning.
The remodeled Center Club featured a lot of high-end finishes in its millwork, tile work, countertops, glass and elsewhere.
“There are millwork ceilings, millwork cabinetry and millwork throughout an entire long, long corridor that’s 80 to 100 feet long,” he said.
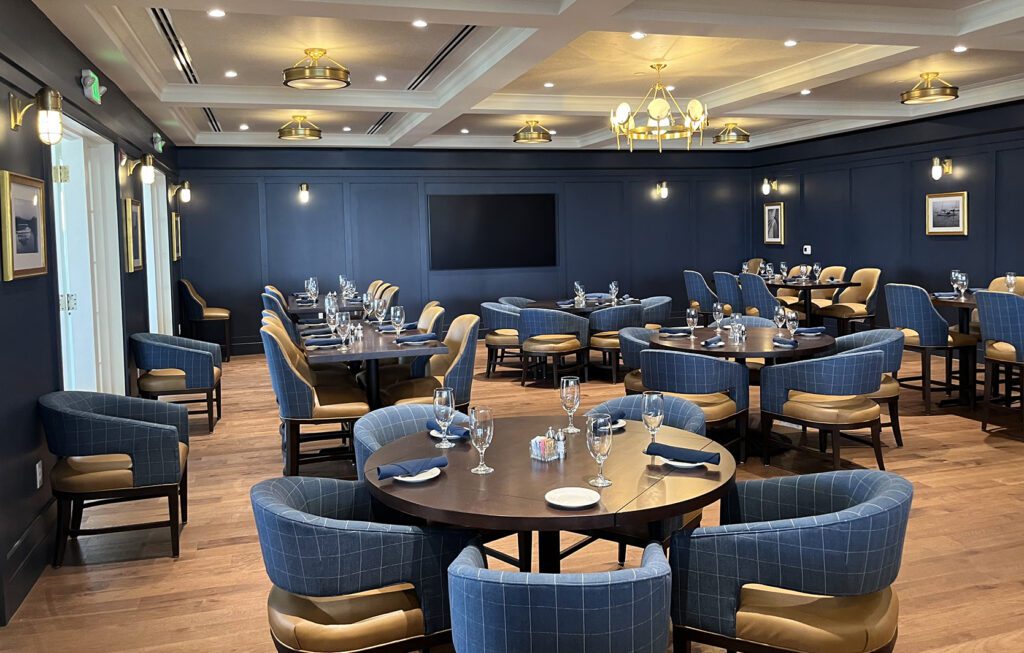
A gut renovation of the dining and bar space at the Baltimore Yacht Club delivered similarly impressive results. Designed around a nautical theme, the project included a lot of teak and Ipe wood, v-groove shiplap walls, a very large bar made from stained white oak, and white quartz countertops.
A key element of the design, however, was a less noticeable feature.
“In a lot of the restaurants that we have worked on recently, there has been a huge emphasis on acoustical treatments,” Ford said. “Restaurant owners are very concerned about noise resonance. We have all been to restaurants where it is difficult to hear people talk even when they are sitting next to you. That can convince people not to come back to a restaurant.”
Consequently, Harvey Construction “worked hand-in-hand with the owners and the architect to find acoustical products that would work with the design and not be too costly,” he said.
Close collaborations
The ability to do value engineering, assist with design and engage in heightened collaboration is vital to many restaurant projects.
“Every single restaurant owner has their own flair, their own vision. But many times, owners either don’t have architects involved in their projects or they have architects involved to a limited degree,” Ford said. “In our restaurant projects, 20 percent to 30 percent of them are design-builds.”
Many others require significant input from the builder on how to execute and refine the design in order to match the project’s vision, budget and schedule, he said. “And every single restaurant owner that we’ve ever worked with has always asked to make some design changes in the middle of the project.”
And it’s not just bespoke restaurant projects that require that close collaboration. Construction of chain restaurants have similar needs.
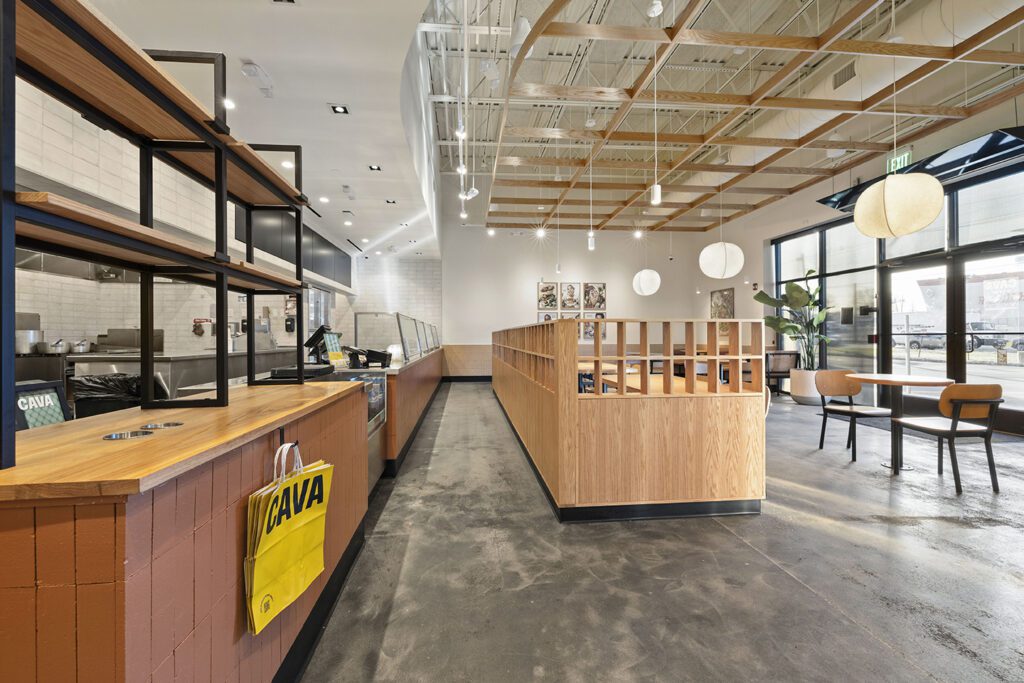
Although the designs of national restaurant chains like CAVA and Raising Cane’s are more prescribed, clients still expect inviting, comfortable spaces. Photo courtesy of Petrie Construction.
Petrie Construction is currently involved in several projects for Raising Cane’s and CAVA.
“Both of those companies are in the throes of nationwide initiatives to develop more sites,” said Adam Petrie, Chief Executive Officer.
Although the designs of those restaurants are more prescribed, details can change from location to location. Raising Cane’s, for example, tailors imagery in each restaurant to reflect the local community.
“You have to really understand their brand and be able to work in lockstep with their CM team, understand their requirements and understand what they are looking to accomplish with each new restaurant,” said Matt Cornelius, Senior Project Manager at Petrie.
As they move into new markets, national chains also rely on general contractors and their teams to understand and address local requirements, such as county regulations on the placement of grease traps. They also rely on GCs to assemble reliable, impressive teams of subcontractors in each new market.
“What you are seeing more in this industry is the search for relationship-oriented contractors and partners,” said Jeremy Bragg, Director of Construction Services at Petrie. “Owners are looking for a general contractor who is going to bring them value beyond any individual project. We have to become their partner, their resource and create a team that will deliver on their projects.”
Petrie Construction has utilized “The Petrie Way,” its core values, to create those relationships with national restaurant chains and to partner with subcontractors who can best execute those projects, Cornelius said.
“As we find ourselves expanding our reach across the country to build these restaurants, we are carrying some of these subcontractors into new regions,” he added.
Contractors tackle volatile supply chain
From the extensive and changing array of tariffs to declining economic indicators, improved interest rates, high lead times for select products, and a sustained, ample backlog of construction work, contractors are navigating challenging conditions as they source materials and equipment.
So how do companies manage their risk, expenses, project performance and stress levels in the midst of a turbulent supply chain?
Mitigating risk
The first signs of a tariff war prompted Cole Roofing to identify and prepare for possible challenges.
“We had constant communication with vendors to understand the impacts they were anticipating,” said Bill Cole, President. For example, “we knew one underlayment product we use comes from Canada. So, we were asking the vendor: What are you doing? Are you moving more inventory across the border early? What kind of price increase could the tariff create? What alternative products could we source within the United States?”
The second step in Cole’s communication plan was for its legal team to determine the best language to put into contracts to address the risk tariffs posed to project costs.
The third step was to start talking about tariffs to customers.
Price fluctuation became “a heightened topic so the discussion with the customer was do you want to take on that risk or do you want us to take on that risk,” Cole said. “If the customer wants to assume the risk, then let’s set an allowance aside and create criteria for using that allowance so everyone understands the potential impacts. If the customer doesn’t want to take on the risk, then I have to be responsible and say I have to charge you more because I don’t know how much this product will cost by the time you’re ready to install it.”
Those conversations with customers “were proactive and fruitful,” Cole said. “People at least appreciated the acknowledgement of the challenge we are all facing.”
Cole, who has not yet seen major price hikes, says those preparations have helped his team and his customers “keep a level head” in a turbulent market.
Volatile metals prices
“There has certainly been volatility in steel prices,” said Jerry Taylor, Vice President of Sales and Estimating for Baltimore Fabrication.
While some steel products have seen marginal increases of 3 percent, other prices have shot up 50 percent, Taylor said. “It’s not uncommon to have $150-a-ton increases weekly on certain profiles of steel.”
That has put pressure on the budgets of many projects, “especially jobs bid in late 2023 through 2024 that had a procurement period through the first quarter of this year,” he said. “No crystal ball could have projected these types of increases.”
Some jobs need to be renegotiated prior to release to address the rapid cost increases.
Fortunately, “most owners seem to be understanding,” Taylor said. “They just need you to provide proof of the cost changes and the mills are doing a great job at putting out their announcement letters weekly, letting us know what changes are forthcoming.”
Completing procurements, however, still requires heightened market tracking and communication with general contractors.
“It takes 60, 90, 120 days from final GMP to procurement and purchasing by subs. That’s really challenging for us to manage when vendors will only hold prices for 15 or 30 days,” he said.
To contain its risk, Baltimore Fabrication has adopted a more cautious bidding practice.
“The construction industry is full of risk,” Taylor said. Cost changes are “another component of the risk and being cautious about your exposure is extremely important in this environment. So, if a job doesn’t feel right, if it feels like too much exposure to risk on pricing, I tell my guys let’s not go after it.
Let’s go after jobs that make sense and feel safer.”
Long lead times
At Rosendin Electric Co., “we have seen a lot of fluctuations in the market for copper, steel and aluminum,” said Tony Esteve, Business Development Manager for the MidAtlantic.
Imported steel and aluminum prices have risen due to 25 percent tariffs. Copper has not been subjected to a product-specific tariff. Yet even before tariffs on China and other countries were announced, the cost of copper climbed about 30 percent due to the anticipated impacts of a trade war.
“A lot of copper producers – in China and Chile, in particular – have been slowing production because they believe people will be buying less copper,” Esteve said.
Since metal purchases comprise 20 to 25 percent of an electrical contractor’s costs, Rosendin has long tracked the markets and made large purchases when prices have dropped. The company, for example, made a large copper purchase in early December when the price was $4.02 a pound, Esteve said. By the beginning of April, that price was $5.11 a pound.
Another significant and persistent supply chain challenge is the long lead times for large electrical distribution equipment, generators and liquid-filled transformers.
“The supply chain never really recovered post-Covid,” Esteve said. “A lot of big manufacturers expected a slowdown but market demands grew due to a lot of data center work and renewable projects.”
That challenge, however, has produced a benefit for the electrical industry, he said. Electrical equipment lead times which sometimes exceed the construction schedule for a building, have prompted owners to do early consultations with electrical contractors.
“That’s helped us because we’re seeing opportunities on projects earlier than we would in the traditional pipeline,” Esteve said.
That process has enabled Rosendin to build relationships with owners and arrange the timely acquisition of electrical equipment for projects.
College expands pathways to construction careers
From summer programs for grade-school students to internships with local companies and apprenticeships, certifications, and degrees, the Community College of Baltimore County (CCBC) supports myriad pathways to careers in the construction industry.
Yet the ongoing challenges of attracting enough workers to the industry as well as keeping abreast of the evolving skills required for tradespeople and construction professionals keep prompting CCBC to continue to update and expand its offerings.
At the end of last year, the BC&E Foundation approved a $2,000 grant to support the college’s construction industry training.
The list of construction-related training programs offered at CCBC is enormous. The college offers programs leading to associate’s degrees and credit certifications in Construction Management, Engineering, Engineering Technology, Heating Ventilating and Air Conditioning, and more. It offers workforce training certificates in HVAC/Refrigeration, Building Automation, Certified Apartment Maintenance Technician, Construction Pre-Apprenticeship, and Welding.
The college has partnered with registered apprenticeship providers — both merit shops and unions — representing a wide variety of trades including electricians, carpenters and plumbers – to provide apprentices with classroom training and college credits.
It also provides grade school students with information about and training in construction fields through multiple initiatives. Its Early College Access Program (ECAP) gives high school students a head start on their college education. CCBC’s Pathways in Technology (P-TECH) program connects students from Baltimore County Public Schools with regional employers, including The Whiting-Turner Contracting Company and Johnson Controls Inc. Employers offer students 10- to 12-week internships, serve as mentors and help students pursue careers in engineering and technology. To provide students with early information about career options, P-TECH includes a Summer Engineering Institute for students who are about to enter Grade Nine.
“Great partnerships with companies in the construction industry” have helped CCBC provide students and individuals with compelling information about career opportunities, said Jay Bouis, Assistant Dean, Applied Technology and Logistics at CCBC’s School of Continuing Education.
Those partnerships have facilitated connections between students and employers to place individuals in jobs.
Ongoing interaction with construction-industry companies also enables CCBC to “continually tweak our educational product” to meet current workforce needs, Bouis said. “We have been able to address workforce trends, such as the need for training in computer programs, cybersecurity and automation, including the need for shorter, trade-specific programs. Having the right program that is industry-informed helps place students on a pathway to employment.”
The college has also grown its opportunities for construction workers to expand their skills.
“As a person progresses through their career, they might want to add another certification, another skill. We have short programs and classes to support that,” Bouis said.
Meanwhile, opportunities within Maryland’s college system have made it easier for skilled tradespeople to continue their education and earn degrees.
“There are a growing number of pathways at CCBC from apprenticeships to degrees,” he said. “A person who has completed their skilled-trades apprenticeship, can apply some of that training and work experience combination as college credit. If they decide to pursue a Construction Craft Professional degree, they can enter that program with advanced standing. Apprentices that complete five-year programs are essentially halfway through earning that degree.”
Building the workforce
On April 1st, the BC&E Foundation hosted its annual Builders-In-Training (BIT) Workshop for 150 students from Anne Arundel County Public Schools and Howard County Public Schools at IEC Chesapeake.
Students participated in engaging presentations and hands-on activities in construction and skilled trades, led by BC&E Members Baltimore Fabrication, J.F. Fischer, Whiting-Turner, and our generous host, IEC Chesapeake.
BIT Workshop is a unique opportunity to introduce high school students to the construction industry early, sparking their interest in potential career paths. This year, we also welcomed juniors and seniors who were eager to connect with industry professionals as they explored their post-high school options beyond the classroom.
By connecting students with skilled trades professionals, BIT Workshop transforms classroom learning into real-world career exploration, reinforcing the BC&E Foundation’s mission to build the construction industry’s future workforce through education and programs that support the growth of the Greater Baltimore construction industry.
BC&E welcomes four new members
Enterprise Fleet Management provides clients with an efficient way of managing their vehicles. Enterprise’s transportation solutions improve cash flow, free up credit lines, save time, and allow companies to focus on their core business. www.efleets.com
F.A. Taylor and Son Inc. is a full service, fully credentialed, commercial roofing and sheet metal contractor. With proven expertise in multiple trades and services, F.A. Taylor and Son provides cost-effective solutions for almost every commercial roofing type. www.fataylorson.com
Fallston Supply is an AWI-QCP certified architectural millwork manufacturer. Licensed in Virginia, Washington DC, Maryland and Delaware, Fallston Supply is bonded and self-performs installations. www.fallstonsupply.com
Fisher, Collins & Carter, Inc. is a full-stack site development firm in the civil engineering and land surveying fields for commercial and residential projects as well as large-scale developments.
www.fcc-eng.com