Contractors adopt new practices to meet supply chain challenges
The global pandemic has triggered a variety of delays, disruptions and uncertainties in the construction supply chain and those conditions are prompting some contractors to change their project management processes.
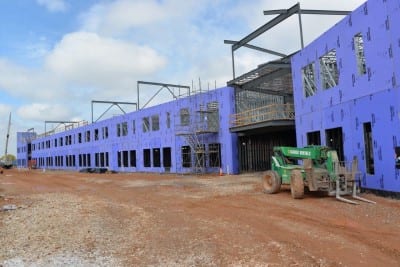
Deciphering all the recent changes in the supply chain “has been kind of like drinking water from a fire hose,” Joe Piro, Vice President and Corporate Director of Supply Chain Management at Gilbane Inc., said on the “Digging Deeper” podcast in late May. “Things are so fluid and changing daily.”
Gilbane’s end-of-May supply chain report indicated that many commodities and products, especially from domestic suppliers, are delivering on normal lead times and without price changes. However, Gilbane warned that many imported products are likely to be delayed. Those include HVAC and MEP equipment from China, Mexico and Germany, lighting from China and Mexico, tile from Italy and furniture components, such as knobs and castors, from China. In addition, uncertainties remain around the supply of domestic lumber and imported steel.
MacKenzie Contracting Company is anticipating “issues and slowdowns with anything imported” over the coming months, said Joe Versey, Senior Vice President of Business Development. “The big things we will be watching are doors, hardware and steel-related products which also affects lighting and ductwork. Those are things you use on every job so you need to get a good idea about lead times because the lead time could exceed the length of the job.”
To contend with those challenging and still changing conditions, contractors are adopting more rigorous processes.
“We jumped on this right at the beginning” of the pandemic, said John Stahl, Vice President at Swirnow Building Systems. “Our team was proactive and quick to assess what projects could potentially be affected and immediately began discussions with manufacturers to ensure that we could address those projects with immediate needs.”
The Swirnow team checked to ensure its standard carriers would be able to deliver product to jobsites on schedule and even made (but never needed to use) a contingency plan to move joist production to an alternate plant.
That kind of direct interaction with subcontractors, suppliers, plants, mills and shipping agencies is becoming a greater part of project management in 2020.
MacKenzie expects to ask subcontractors to verify lead times much earlier in the planning process, Versey said.
Gilbane has developed new processes for sourcing materials. While subcontractors will still acquire materials, “we will need to stick our noses into their business,” Piro said.
Gilbane is talking directly with subs, manufacturers and other companies within the supply chain about price, lead times, delivery issues, potential complications and solutions, he said. The company could also potentially leverage its collective purchasing power with manufacturers to help ensure that subcontractors’ orders receive appropriate priority.
Gilbane is also working to gain “visibility into terminals, into ports” so that it can determine, for example, if a needed supply shipment is in a container that has been placed in quarantine and to negotiate with shippers to ensure that essential supplies make it onto a truck on time, Piro said.
Through that added collaboration, the company is also working to develop keener insight into emerging supply chain issues, he said. For example, delayed deliveries of lighting equipment from China and Mexico could result in more orders being shifted to American manufacturers. But project teams depending on those orders will need to be aware of any developing backlogs and lengthening lead times at those manufacturers.