Data center projects demand expert construction on hyper speed schedule
For Baltimore Fabrication, the process of completing more than a dozen data center projects within four years provided intense, on-the-ground education about how to thrive in a high-speed and highly demanding market segment.
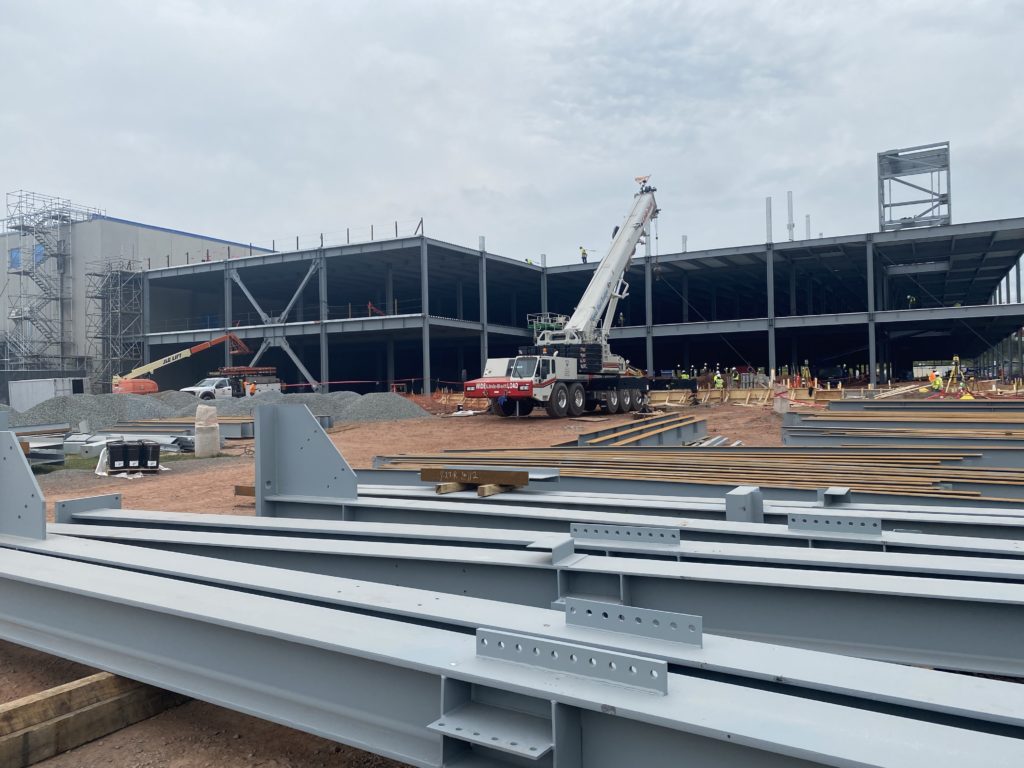
“These projects are hyper accelerated. The customer needs the data center functioning to make money,” said Mark Rich, President of Baltimore Fabrication. To meet those pressing needs, contractors “need to learn quickly and incorporate those lessons into your preconstruction and construction processes.”
Those conditions can require contractors to shoulder heightened responsibilities for design and scheduling, increase project staffing, improve their supply chain, implement new prefabrication processes, master the delicate process of operating in live facilities and rapidly accommodate large, mid-project changes. Expert contractors, however, have access to a large, varied and growing array of projects, ranging from new 250,000-square-foot data centers by hyperscalers to strategic retrofits of 5,000-square-foot facilities. And industry watchers say the amount of data center work in Central Maryland is poised to expand.
“When I go to Ashburn or Manassas, I particularly like seeing that we have four or five cranes in the air [at data center sites] down a two-mile stretch of road,” said Chris Gregory, Executive Vice President at SteelFab Inc., Baltimore Fabrication’s parent company. Even though Northern Virginia already has one of the highest concentrations of data centers on the planet, “we don’t see the pace of construction slowing down in the next few years, and I hear that Maryland is going to be the next location for future data center development.”
Virginia has attracted data center developments through sales tax reductions on those projects.
“Maryland recently passed an incentive program to compete with Virginia on that front so I think we will see more data centers in Maryland as a result,” said Jeremy Bray, who is the national mission critical core market preconstruction leader for DPR Construction.
Those Maryland-based developments will require contractors to meet the hallmark challenges of data center construction and master some emerging trends.
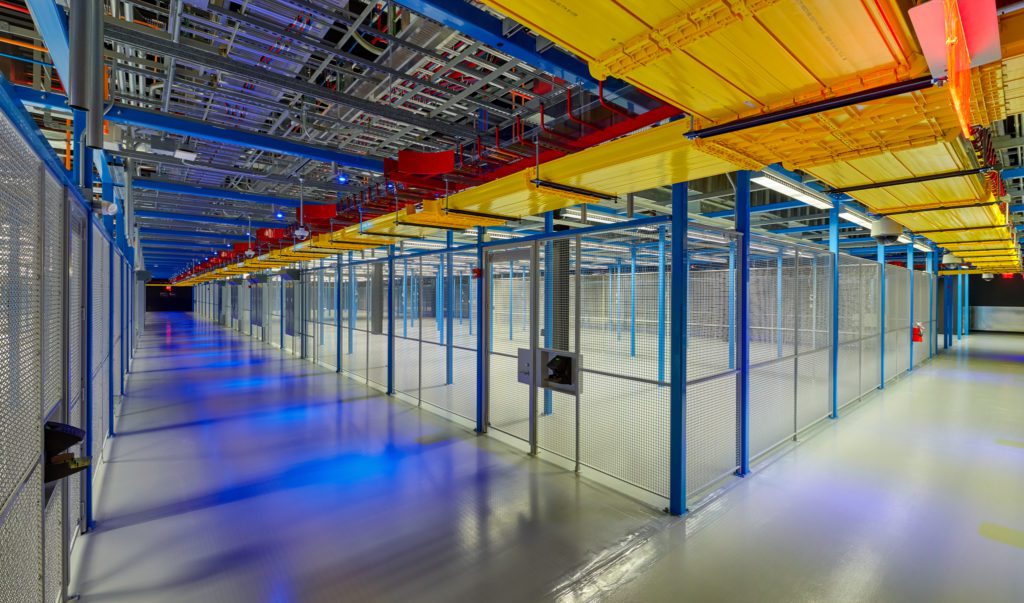
With large, greenfield data center projects often lasting just 11 to 18 months, structural steel contractors, MEP firms and some other subs are brought onboard and released when construction documents are only 30 percent complete, Gregory said. That requires contractors to assume greater design duties and release their own drawings and supply orders unusually early.
During its early data center projects, Baltimore Fabrication developed typical details for interior stairs, railings and ladders as well as structures for generator yards, and began expediting submittals to project design teams in order to start production quickly, Rich said. Those ‘typical details’ also enabled the company to quickly accommodate changes in project design or scope, such as buildout expansions to serve a newly-signed tenant.
“Steel allows us to create modular structures that can be reconfigured and added to in the future,” Rich said. A new tenant necessitates “increased capacity which often means doubling the generator yard and ‘double stacking’ the generators so we need to reconfigure, fabricate and install new platforms, stairs and railings quickly!”
Those processes enabled Baltimore Fabrication to complete the contract on its “largest data center to date in under 90 days,” said Scott Foreman, Executive Vice President. “Due to the schedule, we did not have time to obtain field dimensions of existing conditions. Our work was fabricated based on hold-to dimensions which were coordinated with our design model. We built six stairs and over 1,000 linear feet of railing with limited field modifications.”
In the midst of that compressed schedule, project teams must also satisfy varied and evolving needs of individual data center projects.
“One trend we are seeing lately is clients trying to squeeze as much capacity as possible out of their existing data centers,” said John Brockwell, Vice President for the Mission Critical, Building Infrastructure and Commissioning Practice Group at Bala Consulting Engineers.
In those cases, Bala assesses the existing loads and available capacity of the utility service to an individual data center, calculates the additional capacity needed to support the power and cooling requirements of the envisioned expansion, and then develops a plan to increase the building’s critical systems infrastructure to support the client’s needs.
“A lot of the work we do now is infrastructure upgrades within live facilities and one of the critical aspects of a data center is once it is operational, you can’t turn it off,” Brockwell said. “So we work with the client to figure out how to make the upgrades while maintaining full operations.”
The intense MEP needs of data centers are changing in other ways.
To sustain continuous operations, data centers have typically required onsite generators to provide full energy backup in the event of an electrical outage. To meet that need and increase their sustainability, more data center owners are adding onsite generation to their projects, typically with hydrogen fuel systems, Brockwell said.
At the same time, some other data center owners are “moving to reduce redundancy requirements,” Bray said. “They place less emphasis on the building being up all the time…because they are shifting to software solutions. If a data center goes down, the software shifts the operations to cloud platforms.”
To lower energy and water use, select data center owners are establishing new operational standards for their properties.
“There are some bleeding edge technology companies that want to push the ASHRAE standards and operate at elevated temperatures,” Brockwell said. “The equipment in data centers can handle higher temperatures. So some hyperscalers and high tech companies will run their data centers hot and dark. When someone goes in to work in the space, they will cool it off and turn the lights on.”
In the face of climate change, some developers are also hardening their buildings to withstand higher wind speeds and hurricanes. One recent project in Virginia, Gregory said, opted to implement California seismic standards based on the desire of a particular client who was signing a lease for that space.