Expanded collaboration and technology drive road projects
With a scope of work that included 14 structures, a five-span bridge over I-270 and a two-span bridge along an off-ramp, the Watkins Mill Road Interchange project proved demanding on many fronts. The project team relocated streams and an existing utility and jacked and bored a 30-inch pipe beneath the interstate. All work had to be completed on an extremely accelerated schedule in one of Montgomery County’s most congested locations and, as it turned out, during a pandemic.
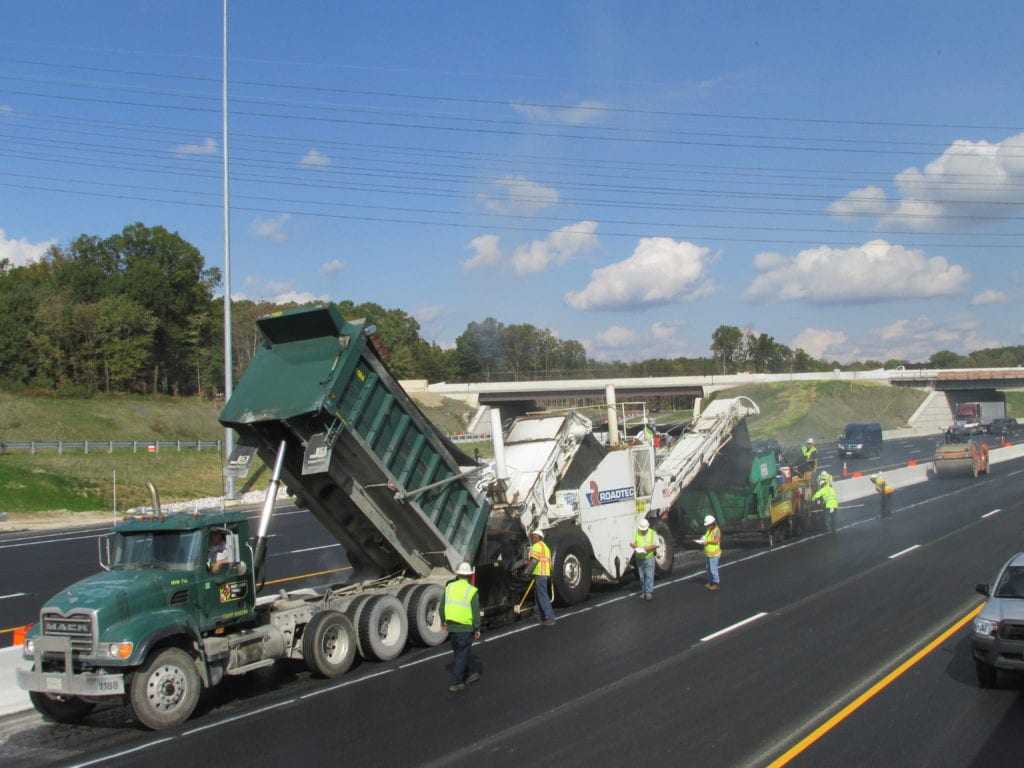
Yet the project team, which included KCI Technologies and Wagman Heavy Civil, completed the massive, $92 million project 30 days ahead of schedule and $10 million under budget. The project has since received several awards, including a Partnering Award from the Maryland Quality Initiative, an Honor Award from the American Council of Engineering Companies of Maryland and an Excellence in Infrastructure Award from the Heavy Construction Contractors Association.
While the accomplishments of the team were outstanding, the Watkins Mill Road interchange lined up with the daunting scope and complex challenges of current bridge and road projects. As the state begins to increase its transportation contracting and federal legislators debate an infrastructure package, contractors will need to be ready to tackle some changing requirements in bridge and road projects.
Contracting practices
Increasingly, projects in Maryland, especially larger ones, are using design-build delivery and awards are placing “more emphasis on value, road performance and what is best for the riding public, rather than simply being a low-bid award,” said Jeff Graf, Senior Vice President of Asphalt Operations at Gray & Son.
That trend is both liberating contractors from some rigid construction requirements and requiring them to collaborate more extensively with engineers and propose options to improve project costs, efficiency and performance.
The process, Graf said, lets contractors leverage “your ingenuity and experience to determine how to move projects faster and deliver quality. It allows contractors to utilize their resources, people and equipment to the best value.” Achieving that capability, however, has also required companies like Gray & Son to expand their project management staff.
At the same time, governments are opting to turn some large ventures into Public Private Partnership (P3) projects, said Dana Knight, Vice President and Transportation Regional Practice Leader at KCI Technologies. For example, the State of Maryland has appointed a manager for P3 projects in the I-270 Corridor — a move that is expected to trigger the start of several bridge and highway projects.
Design engineers land on “a bit lower tier in P3 situations. Normally, we would be working for the owner, State Highway Administration. In P3s, we could be working for the contractor who, in turn, is working for a financing entity,” Knight said. “The projects are typically fast paced with pretty intense schedules and we have to sharpen our pencils to make sure we have good, competitive pricing.”
High-tech blacktop
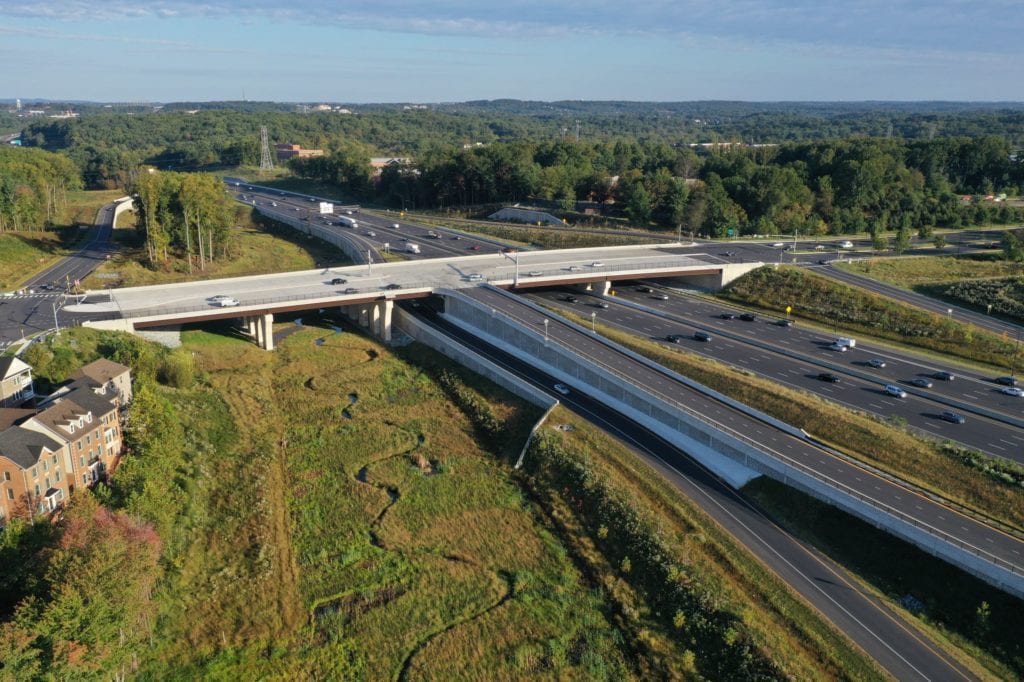
Road and bridge projects are steadily moving away from paper plans and specifications to 3D digital models, Knight said. “The 3D models make it easier to see conflicts, such as a spot where fill would be covering a utility… Another cool thing about 3D is when you go to public input meetings, you can show realistic graphics and animations, so the public can see how cars will move through an intersection or how a new road, landscaping and sound walls will look in their neighborhood. In the future, we will do just about every project in 3D.”
Ultimately, those digital models could feed into the machines that complete the paving.
“With GPS systems, laser guidance and drone technology, our projects are really becoming high-tech projects. Most current equipment is fully automated,” Graf said.
For example, rollers perform “smart compaction” which constantly monitors the density of the subbase and adjusts the level of compaction to produce consistent, optimal conditions. GPS-equipped pavers can not only lay pavement according to project design but automatically adjust to changes in the road elevation.
Graf predicts that autonomous vehicles will become standard for paving crews in the next three to five years both to improve crew safety and to compensate for the lack of skilled tradespeople.
Building a better street
Standards for bridge and road projects are also increasing.
“Years ago, big rocks, little rocks and hot sticky stuff was our asphalt mix. Now we are always looking to improve the performance of our materials,” Graf said.
By adjusting rock shapes, additives and other elements, the paving industry has expanded the lifespan of roads. It has grown from 7-10 years two decades ago to 15-18 years currently. Contractors now strive to create “perpetual pavement” that can last 30 years before requiring a one- to two-inch resurfacing.
Environmental requirements, especially for stormwater management around the Chesapeake Bay, have also changed. Consequently in congested areas, new interchanges, road widening and other projects require new forms of stormwater management, such as underground storage, Knight said. “Meanwhile, environmental and quality of life concerns are resulting in more requirements for ‘complete streets’ which include safe space for pedestrians and bicyclists.”