Fast projects, labor shortages heighten safety concerns
On a data center construction site in Northern Virginia, the opportunities, demands and hazards of the current construction environment are evident. Like so many other projects, the work is driven by high demand for rapidly completed facilities. But the work is also periodically interrupted, re-sequenced or accelerated due to the slow, erratic operation of the supply chain. Those schedules can take a toll on workers.
“At that one jobsite, they have hundreds of electricians working,” said Eric Charlebois, Mid-Atlantic Manager of HazTek Inc., which is providing safety consulting services to the project. “They just got word that they are moving to seven, 10-hour shifts per week, including overnight shifts. That’s a month of daily 10-hour shifts and some of those individuals are driving from West Virginia, Frederick or Hagerstown. You are going to have fatigue and fatigue brings an onslaught of safety concerns.”
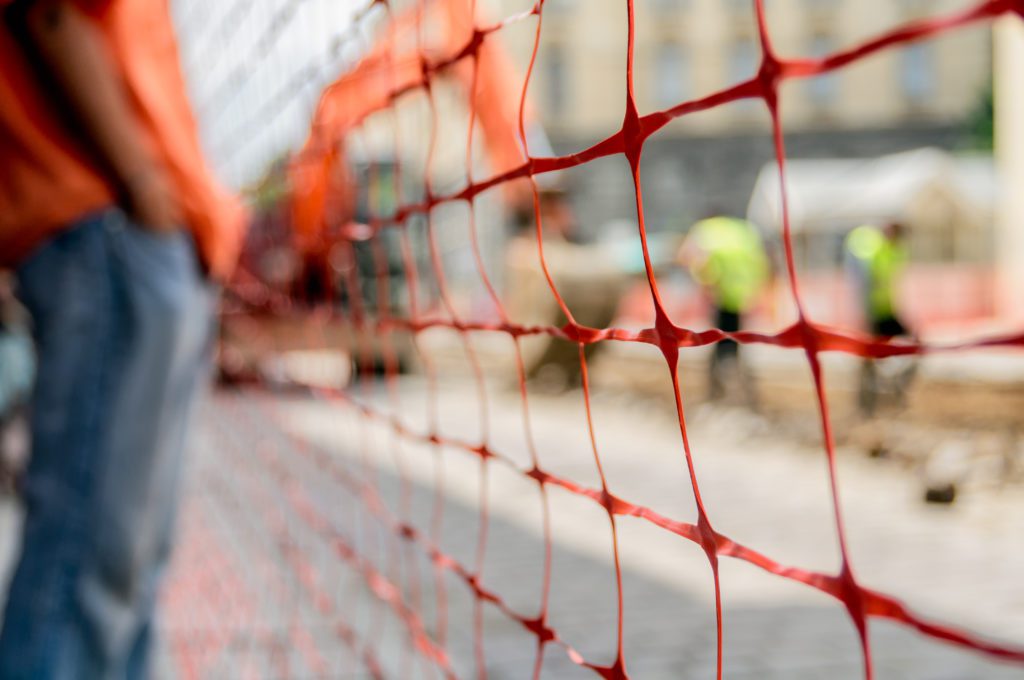
Ensuring safe operations on construction sites may be an age-old activity but working conditions within the industry make it an endlessly challenging pursuit. In the face of today’s demanding schedules, labor shortages and countless variations in site conditions, safety experts are urging builders to review and strengthen their safety protocols.
Measures that improve jobsite safety come in many forms and they don’t have to be enormous efforts to deliver significant benefits.
Plano-Coudon Construction, for example, adopted a motto of PC SAFE (Safety Awareness First Everyday) and gradually implemented practices to both increase workers’ focus on safety and strengthen safety protocols.
Those practices have included “engaging third-party safety inspectors and doing random, internal inspections by someone who isn’t on the team running the project,” said Thomas Koch, Director of Risk Management and Safety. “It provides a different set of eyes looking at the site through a different lens. When you are on a jobsite, you could walk by something over and over again and, because you are so familiar with it, not realize it’s a safety issue.”
Sometimes the overlooked safety hazard is something as mundane as housekeeping, Charlebois said.
“Housekeeping is probably one of the biggest challenges that safety professionals see on jobsites. There is wood and other materials scattered all over the place. We’re not trying to be neat freaks, but if you have good housekeeping on a jobsite, a lot of hazards are not hidden anymore,” he said. “If you have laid a piece of plywood over a three-foot by three-foot hole and everybody is walking over it and it is exposed to the elements, Murphy’s Law says that in time that plywood is going to break and someone is going to drop through that hole.”
Plano-Coudon has also started “utilizing new KPIs to monitor safety on all projects and determine which projects have higher safety exposures so we focus our attention on meeting everyday safety needs while also recognizing the uncommon ones,” Koch said.
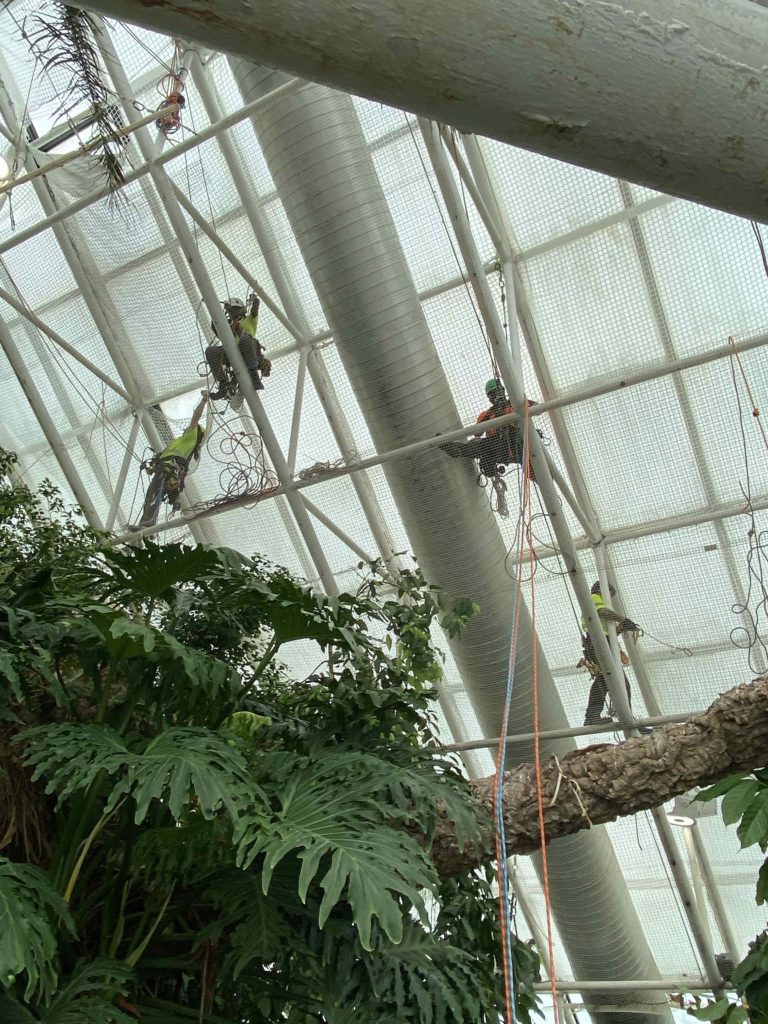
Those key performance indicators can be as routine as verifying completion of regular, required inspections to establishing and tracking added safety protocols that are required during unique activities not encountered on a daily basis.
“One project we are doing in Delaware is right on the water which means there are extra rules you need to understand and follow,” Koch said. “For example, some individuals may have to wear a life jacket even though they are working on land. A worker could be in a situation where if they were working on a ladder and fell over, they would land in the water.”
Similarly, Plano-Coudon has implemented heightened planning and education for safety at the National Aquarium in Baltimore where it is currently replacing the glass in the aquarium’s iconic glass pyramid. The project’s distinctive safety requirements include ensuring that workers are properly trained, certified and experienced to operate in harnesses suspended from the pyramid’s rafters. Plano Coudon must also ensure that work is carefully sequenced and workers properly educated to work safely alongside a large crane on the aquarium’s pier.
In both unique and commonplace projects, robust communication practices can greatly improve safety, said Jason Sears, Field Operations Manager for Diversified Safety Services. A regular morning huddle with superintendents and foremen to review operations that day – especially when deliveries, sequencing or other plans are shifting – can alert teams to anticipated safety issues and review needed safety protocols.
“More of our clients are doing weekly safety meetings,” Sears said. “They push out a topic which could be ladders or safety glasses or electrical safety, and have their teams in the field review that topic.”
Simple, 15-minute orientations for subcontractors, which cover the required training and safe operating practices for machinery and equipment they will be using onsite, can also deliver surprisingly large benefits, Sears said.
While visiting construction sites, “I have run into a lot of people who don’t have the proper training. That has become very prevalent over the past year,” he said.
The training shortfall has included individuals who didn’t realize they needed to learn about fall protection before engaging in work they were already doing and individuals who were operating equipment they had never been trained on.
“You run into guys who automatically assume that because they know about forklifts, they can operate any kind of lift,” Sears said. “But a forklift is a whole different animal than a scissor lift. People require a lot more mechanized equipment training than they think.”
Increasingly, Sears added, companies need to provide all of that safety training in both English and Spanish.
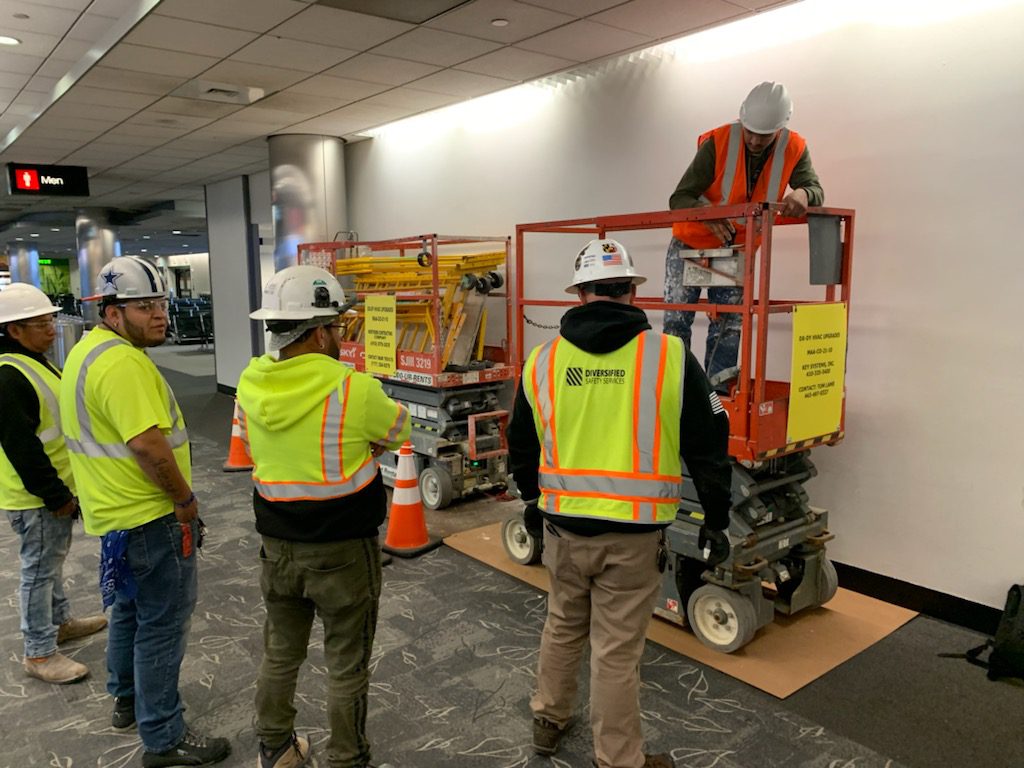
A variety of other practices and products — including drones, software programs and QR codes — can boost safety on a jobsite. But there isn’t a ‘one size fits all’ approach to optimizing safety practices in all construction companies, Charlebois said.
To determine what safety initiatives will work in a company, “you need to take a deep, soul-searching review of what your company is doing and listen to employees from your lowest level all the way to the executives,” he said. “I deal with this a lot. People don’t want to air their dirty laundry even inside a company. But guess what, that dirty laundry will help you in the long run to identify your problems and address them.”
Safety professionals and many construction industry peers readily share insights into how to better deal with situations, he added. “Don’t be afraid to consult an outside source. Talk to other companies within BC&E. When you are talking about safety, even the most tight-lipped executive will probably open up.”