From bio hazards to big data: Life sciences projects get more complex
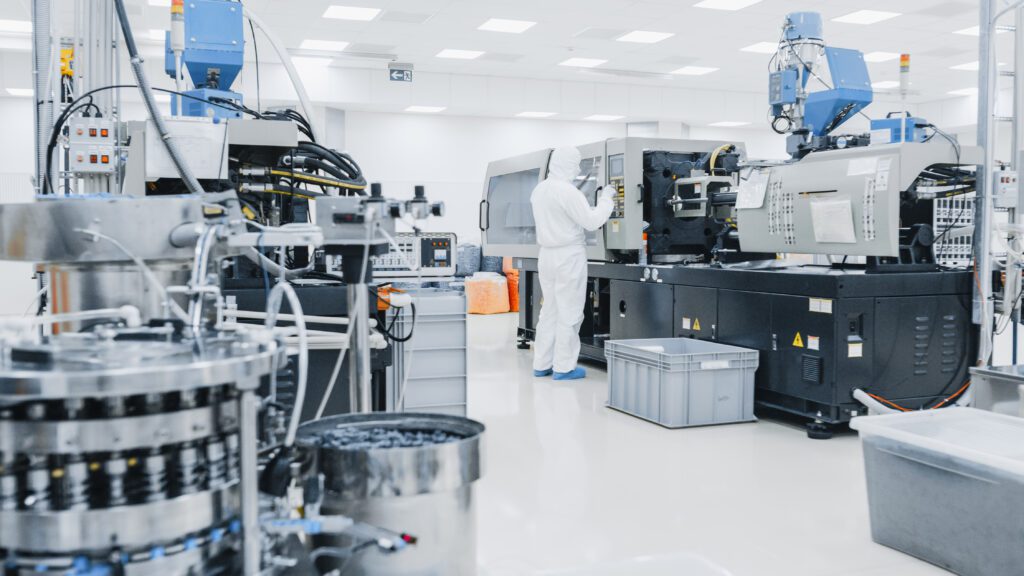
From building state-of-the-art laboratories inside century-old institutes to meeting the high-speed needs of medical researchers and readying biopharma manufacturers for robotics and AI, the life sciences market presents construction teams with extraordinary challenges. And in Maryland, life sciences construction is both growing and becoming more complex.
Projects currently in planning or underway include the Johns Hopkins University Belward Campus (a 57-acre development in Rockville that will include 757,000 square feet of private lab space) and The Labs at Jefferson Tech Park (a 500,000-square-foot life science research and manufacturing campus in Frederick). In October, JHU announced plans to construct a new life sciences building at Broadway and East Monument to anchor a new “Life Sciences Corridor” in East Baltimore. In February, AstraZeneca announced a $300 million plan to build a state-of-the-art manufacturing facility for its stem cell therapies in Rockville. Meanwhile, a stream of renovation and new construction projects for public and private laboratories and manufacturing spaces are happening around central Maryland.

At Gilbane Building Company, project teams have been managing multiple life sciences projects, ranging from a few thousand square feet to a few hundred thousand square feet. They include Biosafety Level (BSL) 2 and 3 research and development laboratories, Good Manufacturing Practice (GMP) and cGMP (Current GMP) manufacturing facilities, vivariums, and high-containment facilities.
“Adaptive reuse of offices into research and development labs has become more prevalent. We have even seen some office conversions to manufacturing space,” said Scott Earley, Project Executive at Gilbane.
Office-to-life science conversions are complicated by limited deck-to-deck heights and the need to fit an entirely new realm of infrastructure — including lab gases, process water, data lines, specialized air systems, monitoring equipment, and redundant infrastructure — into a building that was designed to support offices. However, any construction or renovation of laboratories and manufacturing suites is packed with design, engineering and construction challenges that require specialized solutions.
“These projects require strong virtual design,” Earley said. “We draw everything out in 3D and we get pretty detailed. We like to see each run of pipe and ductwork… Since a lot of our life science projects happen in occupied facilities, we also use our virtual capabilities to work out logistics and show how we are going to conduct certain parts of the work.”
Gilbane, which leverages design-assist services on many projects, shares that modeling with trade partners “to work through the design and find the most efficient ways of running that infrastructure,” Earley said. That collaboration has also included “big room” brainstorming sessions where the owner, design team, Gilbane and trade contractors hash out ideas for executing the project.
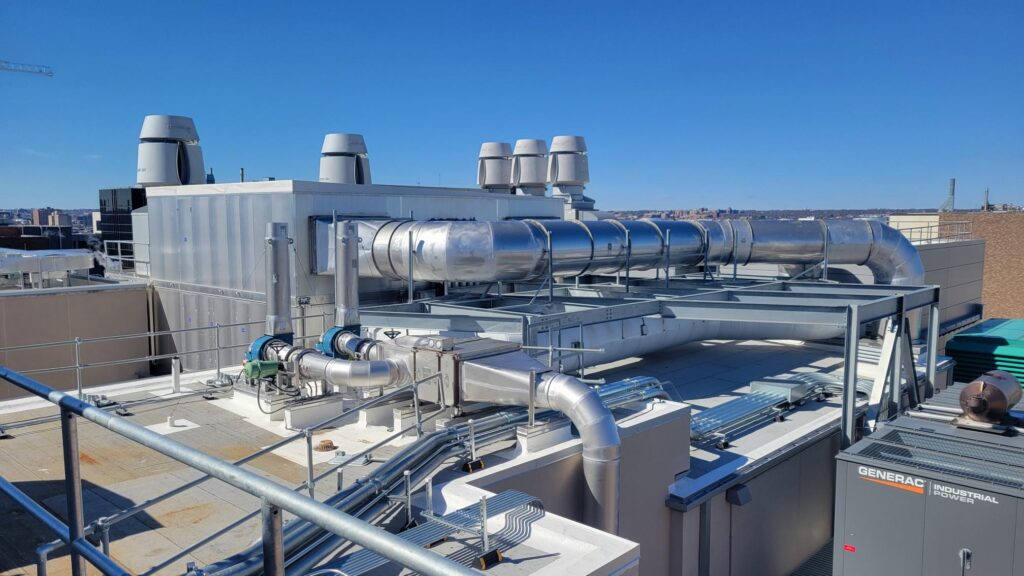
On numerous life sciences projects at Johns Hopkins, University of Maryland and elsewhere, Southern Mechanical has played an expanded design and construction management role.
“It’s great when owners ask us to do design assist and you work with a construction manager that really trusts you,” said Larry Lauer, Vice President. “The mechanical contractor is basically a mini-GC with more subs than anybody other than the GC. We could have 10, 12 or more subcontractors on one project with sheet metal guys, insulators, control contractors, riggers, chemical treatment people, CAD and BIM coordinators, refrigerant guys, core drillers.”
Design assist and expanded collaboration adds time and effort to projects. Southern Mechanical spent a full year working on design assist for the Johns Hopkins School of Public Health East Wing Infrastructure upgrade before starting physical work on the 30-month project. The massive renovation subsequently won multiple 2023 BC&E Craftsmanship Awards.
Mechanical, electrical and other contractors, however, have to be prepared to install and support state-of-the-art scientific equipment, including in century-old buildings like the JHU School of Public Health.
“Newer equipment requires different types of exhaust systems which can mean changing entire exhaust systems from galvanized to stainless steel,” Lauer said. “Depending on the type of research, we could be running specialty gases.”
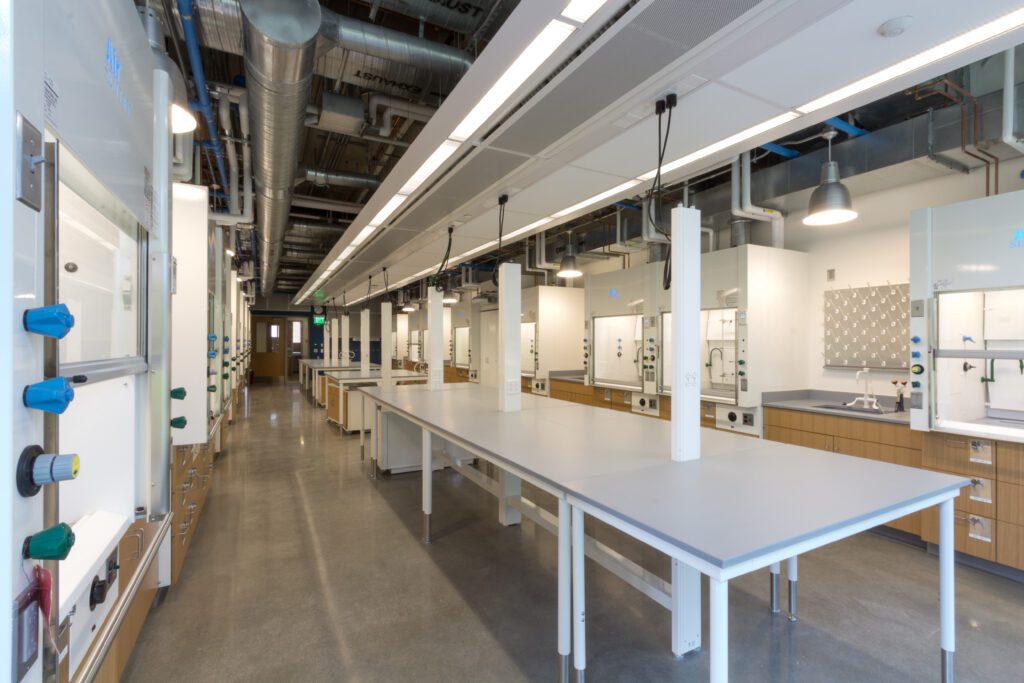
Life sciences facilities require infrastructure redundancy to ensure they maintain a “safe state” during any outage. Projects for Johns Hopkins and some other clients also place a high premium on energy efficiency and include sophisticated heat- and energy-recovery systems.
They also require increasingly advanced building automation systems to provide heightened monitoring, safety systems and isolated environmental conditions, said Steve Petri Jr., Project Manager at Deca Inc.
Over the last three decades, Deca has completed building automation and power installations for life sciences facilities in academic, private and government buildings, including the U.S. Army Medical Research and Development Command at Fort Detrick. Those projects have included BSL3 and BSL4 (the highest safety level) labs.
“Labs are challenging with their requirements and their wiring methods,” Petri said. “Some labs have requirements for room pressures to ensure that if anything leaks, it doesn’t get out of the room. Some rooms have fume hoods and some fume hoods are big enough for people to work inside. Some have wash downs and ante chambers.”
Consequently, contractors need highly specialized and experienced tradespeople to work on life sciences projects, Petri said. They also need detailed knowledge of the requirements and challenges of life sciences projects in order to bid them correctly.
“This is nothing like working up estimates for a standard building. This is a different animal,” he said. “A lot of things aren’t on the drawings. You have to anticipate the problems like running into a shortage of ceiling space for conduit, wiring installations and mechanical systems. And it is going to require more labor — about 50 percent more than a non-life sciences job.”
On two occasions, Petri has seen other trade contractors go out of business in the midst of a life sciences project because they had incorrectly bid the job.

Industry watchers say life sciences projects are about to become even more complex. The industry is set to begin implementing Pharma 4.0 this year – a new standard for leveraging robotics, automation, data analytics, artificial intelligence and other advanced technologies in research, development and manufacturing facilities.
The life sciences/biomedical industry in Maryland is also poised for further growth. Late last year, JLL’s Life Sciences Industry report ranked the Greater DC-Baltimore region as the fourth strongest in the country and capable of growing further if it builds out sufficient laboratory space.
“I don’t think there is a more perfect geography for startups given that we have big government agencies, large-scale education institutions and world-renowned medical institutions here,” Earley said.
In addition, the volume of work done by Contract Manufacturing Organizations (CMOs) and Contract Development and Manufacturing Organizations (CDMOs) is expected to nearly double by 2030.
“We see large-scale companies really looking at CMOs as a way to get their product to market and bolster their production, especially as new treatment modalities get approvals,” Earley added. “There are a lot of products going through end-stage trials right now, so I think we are going to see a lot of large companies get approvals and need more work from CDMO, CMO companies.”