Gardens in the sky: More owners turn rooftops into elaborate terraces
From lines of crepe myrtles and river birch to patios featuring imported tile, fountains, fireplaces, swings and automated sunshades, some urban rooftops have become much more complex construction projects.

Increasingly, law firms, technology companies and other high-end office tenants are seeking out or creating elaborate rooftop and terrace spaces to provide outdoor space for work, lunch, recreation and parties for employees and clients.
Meanwhile, high-end multifamily developers are packing more amenities – outdoor kitchens, lounges, yoga lawns, swimming pools and secluded, plant-filled courtyards – atop mid- and high-rise buildings. That has created a new realm of projects and challenges for landscapers.
When Foley & Lardner LLP decided to renovate its Georgetown offices, the law firm also embarked on a plan to transform 13,000 square feet of previously unutilized roof space into three, high-end terraces. The design would create an expanse of sophisticated lounges and gardens through an intricate combination of IPE decking, concrete and porcelain pavers, artificial turf, custom-fabricated aluminum planters, large trees, shrubs and shade structures equipped with sensors that would automatically retract fabric coverings if winds across the rooftop got too high.
The project required the team from JB Kline Landscaping to meet extraordinarily tight and complex variances, said Nathan Iager, Vice President. The crew first had to turn a sloped, gravel-covered roof into flat terraces and tailor that flat surface to accommodate the different insulation/substrate needs of decking, pavers, turf and other products while also matching existing door thresholds and stairwells.
The team had to work out complex geometry to plan, fabricate and install hardscaping to match the radius of a curved portion of the roof. And the design’s array of pavers, planters, shade structures and more had to line up precisely with every adjacent product or roof edge.
“You start getting into really finite alignments,” Iager said. “If you don’t have a perfectly square layout at just the right tolerance so that you are maintaining joint widths, then everything pushes. Maintaining tight tolerances and staying square across the roof is essential for a well installed final landscape.”
On the Foley and Lardner LLP project and others, JB Kline had to complete careful engineering and logistics planning to ensure that rooftop projects did not exceed structural load limitations and that materials staging or individual design elements did not exceed point load limitations.
At its offices in Tysons Corner, the Appian technology company decided to install a lounge and garden on its fourth-story roof. The signature element in the design would be a modern, cantilevered shade structure.
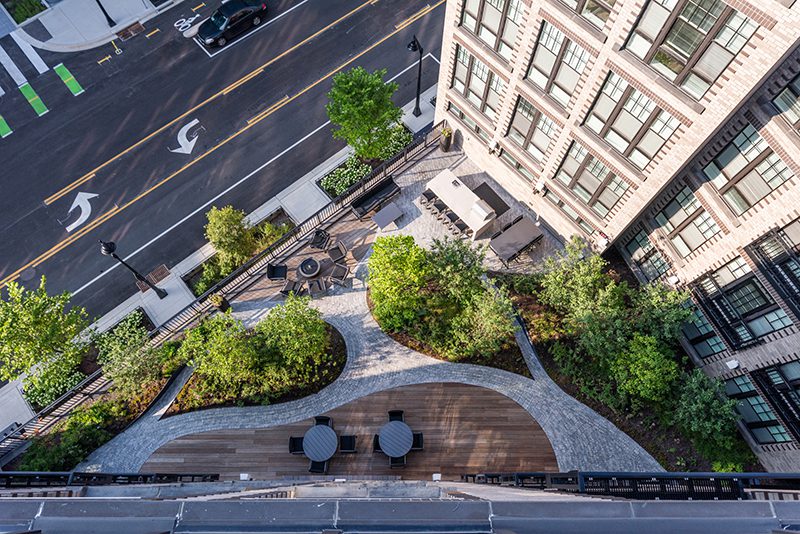
“When this project first came to us, it was a very conceptual, theoretical design,” Iager said. “We brought in a manufacturer as well as an engineer to evaluate the design and began coordinating with the engineer of record for the building. It was a balancing act. We had to have enough structural rigidity in the cantilever design and the right size of metal to span the distance of the structure so that it could withstand snow loads in the wintertime and wind loads — both vertical and lateral. But we had to keep the weight down and make sure the six columns would not exceed the point load or uplift load at any location.”
Installing those structures, terraces, gardens and other outdoor amenities on rooftops presents crews with logistical and safety challenges.
On the Avalon Bay Harbor East project, Live Green Landscape Associates had to crane materials into place for terraces on the 7th, 8th and 24th floors while the building was “skeletal” and a tower crane was still protruding through the 7th floor deck. In addition to staying within point load limits, the crew had to find places to store the materials where they wouldn’t conflict with the work of multiple other trades and where they wouldn’t blow away.
“When you are up on the 24th floor, it’s almost like a different world,” said Justin Jones, Project Manager at Live Green. “You are exposed to all the elements and you can get hit with very strong winds. We had a huge storm come through that produced 80 mile an hour gusts up on the 24th floor. We had to get up there to secure all of our material because we had stacks of foamboard that could have blown away and, of course, they would have landed in the Inner Harbor or on President’s Street.”
Crews had to be especially careful handling materials during installation.
“One of my biggest fears was about a gravel strip, a drain, that went around the perimeter of the 24th floor terrace,” he said. Beyond the edge of that rooftop drain, “it was a straight drop to the 7th floor. My big stressor was that not one rock, not one pebble could go anywhere near that edge and risk hitting somebody below. So, we installed all of those rocks carefully, by hand. Working at heights requires time and patience making sure you do everything right the first time.”
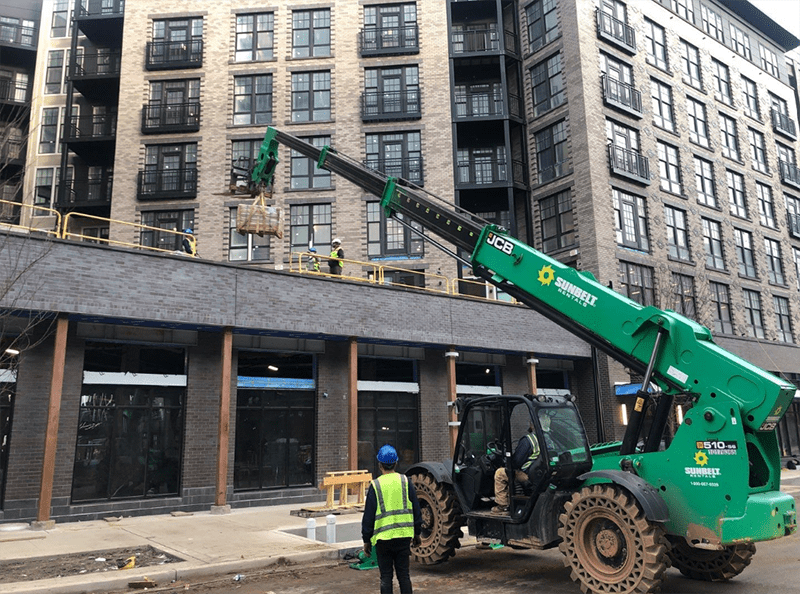
Those rooftop installations, however, have also become much more elaborate, often to create impressive community space and encourage people to move into new multifamily buildings, said Kevin Crawford, Assistant Project Manager at Live Green. The Avalon Bay rooftops included a swimming pool, outdoor kitchen, multiple lounge areas, fireplaces, planters, a green roof and a dog park with custom artificial turf and a drainage system.
At Baltimore Peninsula, Live Green installed a lush rooftop garden that featured custom pavers imported from Turkey. To counter the sharp lines and flat surfaces of the urban surroundings, the garden included curved planting beds with plants and trees set in mounded beds. Walkways that meandered through the space also sloped to match the ‘terrain’ of the beds.
“It created a unique space,” Jones said. “In the area by the fireplace, you feel like you are in a small, secluded courtyard. But it made it very tricky to hit the installation tolerances. We had to coordinate with other trades to make sure that everything that was going beneath the pavers was just right.”