Industrial market remains strong despite challenges
On the site of the former Diamond Point Shopping Center in Dundalk, a construction team led by ARCO Design/Build has started work on a 442,000-square-foot, spec warehouse building.
Despite high interest rates, high construction costs, uncertainties about e-commerce growth and a potential recession, the industrial construction sector remains strong in Maryland and around the Mid-Atlantic. That is prompting builders to adopt some new processes, adjust to new technologies and tackle increasing site and regulatory challenges that face industrial developments.
This spring, Plano-Coudon Construction announced a new option for industrial clients. In partnership with Butler Manufacturing, Plano-Coudon is offering a hybrid construction solution, the LogistX Building System, that combines tilt-up exterior walls with a pre-engineered structure. The system delivers multiple efficiency and cost benefits, said Nick Funk of Plano-Coudon.
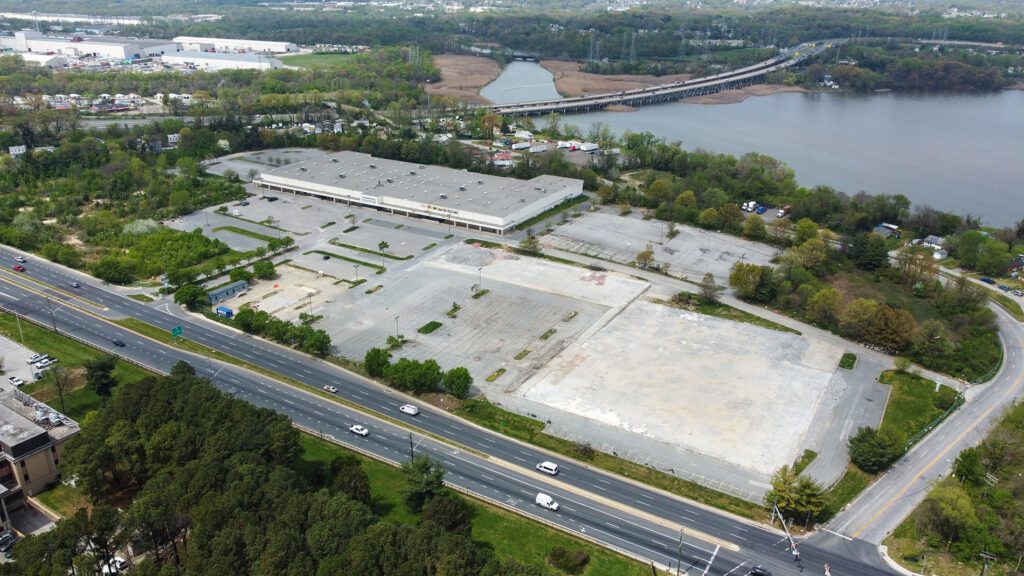
In Dundalk, ARCO Design/Build has razed the Diamond Point Shopping Center and is building a 442,000-square-foot warehouse onsite. Image courtesy of dronegenuity.
“Because the Butler truss purlins and solid web rafters comprise less overall product weight than joist girders and bar joists would, the roof framing system costs less than a traditional system,” Funk said.
The system, which is engineered specifically for warehouses and other industrial uses, saves costs in other ways.
“Because the roof framing system requires less overall height — as much as 12” to 18” in most cases — the total height of the building perimeter walls can be reduced while maintaining the same clear height beneath the steel that would be afforded by a roof framing system constructed using joist girders and bar joists,” Funk said. “The lower wall height saves a lot of cost in concrete in tilt-up construction and some additional cost in pipe and conduit risers, paint, or insulation depending on the project requirements.”
The system also speeds construction “by requiring less labor to install,” he said. “All the connections are bolted and the members are pre-marked and sometimes factory punched for installation without welding and constant measuring. Finally, the galvanized finish results in a fantastic appearance that dull painted bar joists cannot match.”
The hybrid system, which is currently being used on its first industrial project in the Mid-Atlantic (a 150,000-square-foot warehouse in Pittsburgh), can be used in buildings over 1 million square feet and support column spacing up to 60 feet.
Despite high construction costs and economic uncertainties facing industrial construction, ARCO Design/Build has seen no drop in construction levels this year and has even seen some projects which were expected to be postponed, move forward, said Drew Enstice, Vice President.
Technology advances have created new opportunities and changing economies of scale in warehouse projects.
“Sprinkler head technology has evolved so that you can build higher without having to implement an in-rack sprinkler system, and forklift technology which enables you to reach higher rack positions efficiently, is allowing companies to build taller buildings and fit more product on the same building footprint,” Enstice said.
Consequently, popular clear heights have increased to 36 feet for smaller warehouses and 40 feet for larger facilities, he said.
Overall, pricing has levelled off and posted small decreases for some materials, but remains dramatically higher than pre-pandemic costs. However, some prices, such as the price for scrap, are aiding the budgets of some projects.
The Diamond Point project, for example, showed “that it was not significantly more expensive to demolish an existing shopping center than it would have been to build from scratch on a clear site,” Enstice said. “The benefit is you get to use a pre-leveled site that already has utilities. Scrap values are high enough right now to offset demolition costs and we could use the crushed concrete slabs under the new parking areas as opposed to new gravel.”
Building on an existing, commercial site, he said, can also help ease one of the biggest challenges facing industrial projects, namely obtaining development approvals. With many attractive and easy sites already developed in the region, remaining sites often face complications, including issues with stormwater management, forest preservation, limited water supplies, high traffic levels, local opposition, temporary development moratoria or new conservation measures.
Recently, “a specific species of bat went on the protected list in a large part of this region, especially in Virginia,” Enstice said.
New regulations prohibit tree clearing along the bat’s migratory path while the population is moving through this region. Consequently, developers must complete tree clearing before the local migration begins or pause site work for several months.
“It seems like every site we deal with these days has a bunch of hoops to jump through in order to get approvals to start work,” Enstice said. As a result, the start times for many projects can be delayed anywhere from a few months to a year.